How Industry 4.0 could spell the end of unnecessary maintenance
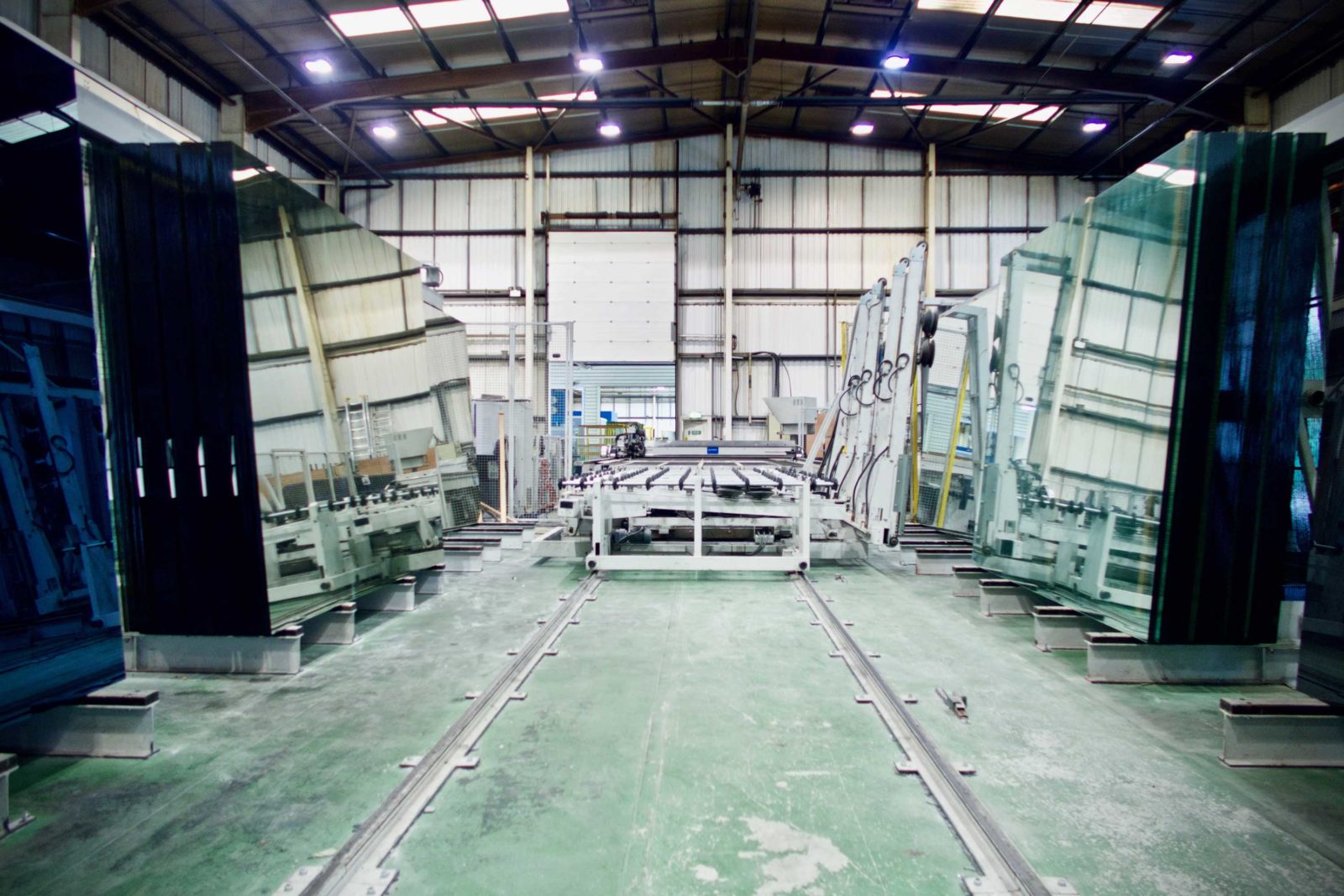
Colin Crow, managing director of digital transformation specialist Sigma Dynamics.
Now, more than ever, manufacturers who have harnessed the power of cutting-edge maintenance technology will be reaping the benefits. This certainly applies in the UK’s glass manufacturing industry, where record demand coming as a result of the lockdown-induced home improvement boom has put pressure on supply chains and production lines.
Being able to operate in a responsive, agile manner, increasing efficiency wherever possible is key to success. With exceptional demand already stretching lead-in times, any additional delay in production could prove costly indeed. Disruption caused by unnecessary equipment maintenance is, therefore, particularly unwelcome.
Senior maintenance engineers know only too well that down-time costs money and can have a knock-on effect throughout the business, hampering productivity, blighting customer satisfaction, damaging reputation and, ultimately, harming profits. To mitigate these risks, preventative plant maintenance is vital.
But while the preventative approach is designed to avoid major equipment failures, and the disruption that comes with them, it can also waste resource. Preventative maintenance leads many manufacturers to set maintenance schedules at shorter-than-necessary intervals, to ensure failures do not occur. Maintaining equipment when you don’t need to, however, costs money. So, what’s the alternative? How can businesses achieve ‘just right’ maintenance?
The answer lies in employing the right combination of self-diagnosing devices, 4G and 5G technology, big data, machine learning and AI technologies to optimise maintenance, swap-out and retirements. Using tech in this way will also enable maintenance teams to focus only on the site visits that add value.
This may sound daunting but, thanks to the new generation of ERP software platforms, it’s never been easier to implement technology and move away from expensive and time-consuming maintenance schedules.
With engineering teams spending as much as 25% of their time maintaining equipment that doesn’t need servicing, a move to predictive, self-diagnosing tech has obvious benefits.
Modern devices tell you their health, let you know when they are in trouble, and provide important feedback such as cycle time and environmental conditions. They also provide data that allows you to determine when a device may fail, when it needs servicing and when it should be left alone.
Predictive maintenance means that, with the help of AI, data analysis and machine learning, you can base decisions on the real-time data that your self-diagnosing devices produce.
The advantages are numerous here. Targeting predicted failures before they happen keeps production rolling, achieving positive results for both internal and external customers. At the same time, avoiding unnecessary maintenance work saves time and money.
On top of this, today’s self-diagnosing tech also tells you when it’s time to swap out and when it’s time to retire apparatus, with greatly improved accuracy.
Digitally optimised maintenance shouldn’t happen in silo. It should exist as part of a connected enterprise, which connects technology, processes and people across the entirety of the business. This helps to unearth a whole new level of insight, regarding the way in which each element of the business impacts upon overall performance.
Connecting across functions in this manner leads to joined up data, shared processes and understanding. This constantly refreshed intelligence can then be turned into action, with the results clear to see via shared reporting dashboards.
Digital transformation should be a phased process, an evolution of a business’s existing systems and processes.
It’s certainly not a case of out with the old and in with the new overnight. There’s no need to break the bank to achieve big results, either. In the maintenance arena, existing equipment can often be upgraded, to enable data collection and analysis. Current data platforms can be migrated across into AI and analytics-friendly systems, and new tech can be integrated into existing IT platforms.
Most importantly, specialist providers are available to manage every stage of the process smoothly and efficiently, based on the best practice solutions for your sector.
As glass manufacturers continue to switch on to the power of tech to optimise their operations, now and in the future, it’s vital that the maintenance function is part of this digital revolution.
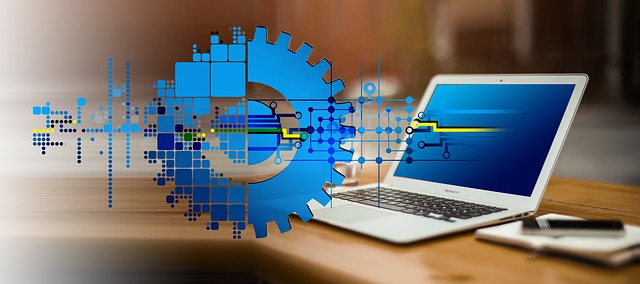