Heavy metal
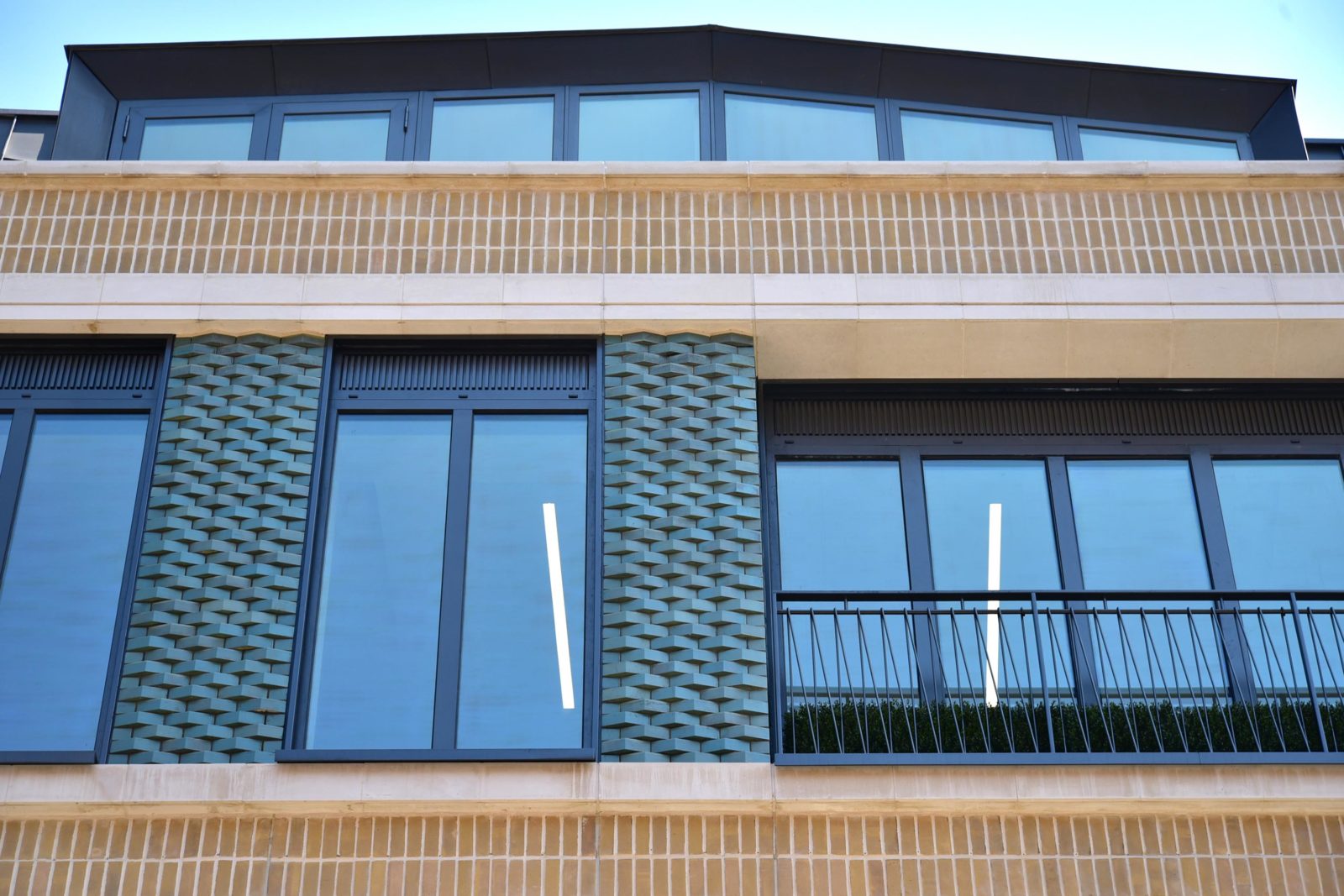
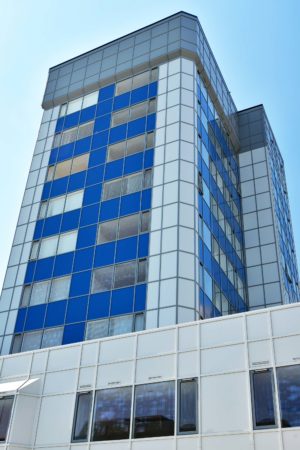
When Tom Kenney was seeking a powder coater to support his new business venture, Kencar, he turned to Birmingham-based, Vertik-Al. Having come across the long-established powder coating specialist in a previous career, Tom was keen to understand what Vertik-Al could offer a new entrant into the fabrication and facade industry.
It was Vertik-Al’s dedication to quality that first sparked my interest. A former employer would out-source to them when a job required a guarantee. In my opinion, this made Vertik-Al a good fit for Kencar, underpinning our commitment to deliver high-quality bespoke architectural metal work.
Vertik-Al offers 25-year supplier backed guarantees on a range of colours and is the only applicator in the UK and Ireland to hold the GSB International quality seal for Approved Coated Aluminium. It is also one of a handful of applicators to boast membership of the product certification scheme, Qualicoat.
Established in 2016 and employing 25 people from the local area, Kencar has grown rapidly in recent times and is quickly gaining a reputation for being a trusted supplier of metal work to the architectural facade industry.
We specialise in insulated panels, using one of the largest pressure bonding machines in the country. We can also fabricate various rainscreen and interlocking panels.
Fascia and soffit systems, copings, cappings, sills, brackets and flashings make up the remainder of our product offering.
Vertik-Al is renowned for its fast-turnaround, and our close proximity (we’re just 20 minutes away) means we can maximise this. If we need a job doing quickly, we know it can be on the powder coating line within hours.
The team keep us updated on where jobs are in the production process allowing us to coordinate the most efficient drop-off and collection times.
We have directly benefited from Vertik-Al’s recent investment in new powder coating equipment, including two new horizontal plants and an upgraded booth alongside new automatic powder guns on line two. This investment has significantly reduced the time taken for colour changes, boosting the speed and efficiency of the entire powder coating process.
The new equipment is delivering incredible results: the quality of the application and finish is outstanding, across matt, gloss and textured coatings.
Glass has been a dominant feature in the facade industry for many decades but changes in architectural trends have led designers and architects to seek alternative materials and finishes; something we have experienced first hand.
The majority of our work is destined for London or city-centre projects in Manchester and Birmingham. We supply high-end apartment blocks, hotels and large commercial buildings, primarily. This means we are at the forefront of cutting-edge design; involved in trend-setting projects which push the envelope of aesthetics and style.
Last year, powder usage figures shared by Vertik-Al revealed that its lines were dominated by shades of grey. This usage has been directly influenced by customers such as Kencar – there’s been an awful lot of grey over the past few years.
However, we are starting to see a rise in metallic finishes, especially bronze. Architectural facade designers are exploring statement exteriors and detailing using metallics or standard colours like pewter and white in a metallic finish.
Designers also appreciate that bronze metallic powder coating is a successful alternative to the finish achieved by anodising; it replicates the look without the need for anodisation.
We have an incredibly good relationship with Vertik-Al. Its reliable service and support, particularly during the pandemic, is invaluable and directly impacts our ability to deliver high-quality metal work on-time and in-full.
Its supplier-backed guarantees, accreditations and certification are an important factor in the specification process and help us to stand apart from the competition.