Window Widgets showcases sustainability
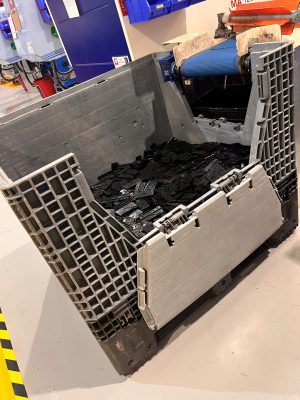
As part of its environmental mission, Window Widgets says that its injection moulding process is as environmentally friendly as possible, from the raw materials through to the processes used to the packaging the products are distributed in.
Focusing first on the materials, Window Widgets has curated a series of eco-friendly options, which it claims are better for the environment whilst not compromising on quality. Endcaps, run-up blocks, bridge packers and corner protectors are just some of the products crafted from recycled polypropylene, all of which aim to reduce waste and allow for an eco-friendly production process.
In addition, the team has the highest quality machinery in operation to ensure that it is able to be as sustainable as possible throughout the moulding manufacturing process. One of these key processes, for example, is the moulding of corner protectors – a key product used to protect the windows during transit from fabricator to installer to homeowner.
The creation of these corner protectors begins with the raw material – recycled polypropylene – being fed into the hopper. From there, the pellets are carefully dried to remove moisture, which helps eliminate streaking lines, commonly known as tiger lines, on the finished product.
Next, the appropriate masterbatch is added to introduce the correct colour for the specific product being moulded. The dried pellets then enter the barrel, where they are heated to a temperature range of approximately 210-250°C. Once melted, the material is injected into the mould cavity, ensuring precise shaping and consistency. The injection moulding process is swift, with a cooling cycle time of just 40 seconds per batch of 12 mouldings, allowing Window Widgets to produce between 10,000 and 11,000 units within a 12-hour shift.
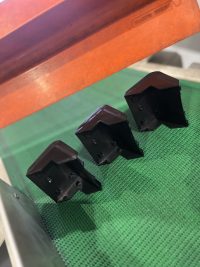
To guarantee the highest standards, rigorous quality checks are conducted throughout the process. The first-off moulding is carefully examined against master samples, scrutinised for any defects such as flash (excess material), sinking (dips in the moulding), or short shots (incomplete moulding). Following this, quality inspections are performed every two hours, with records maintained in their quality lab for reference and traceability.
In addition to its sustainable materials and manufacturing approach, Window Widgets ships its products in reusable packaging.
James Hopkins, moulding manager at Window Widgets, commented: “Sustainability is at the heart of what we do. Being able to repurpose materials and reduce waste aligns perfectly with our net zero and zero-to-landfill goals. Every step we take in improving our injection moulding process brings us closer to a greener future.”