Lower cost manufacture. Lower emissions.
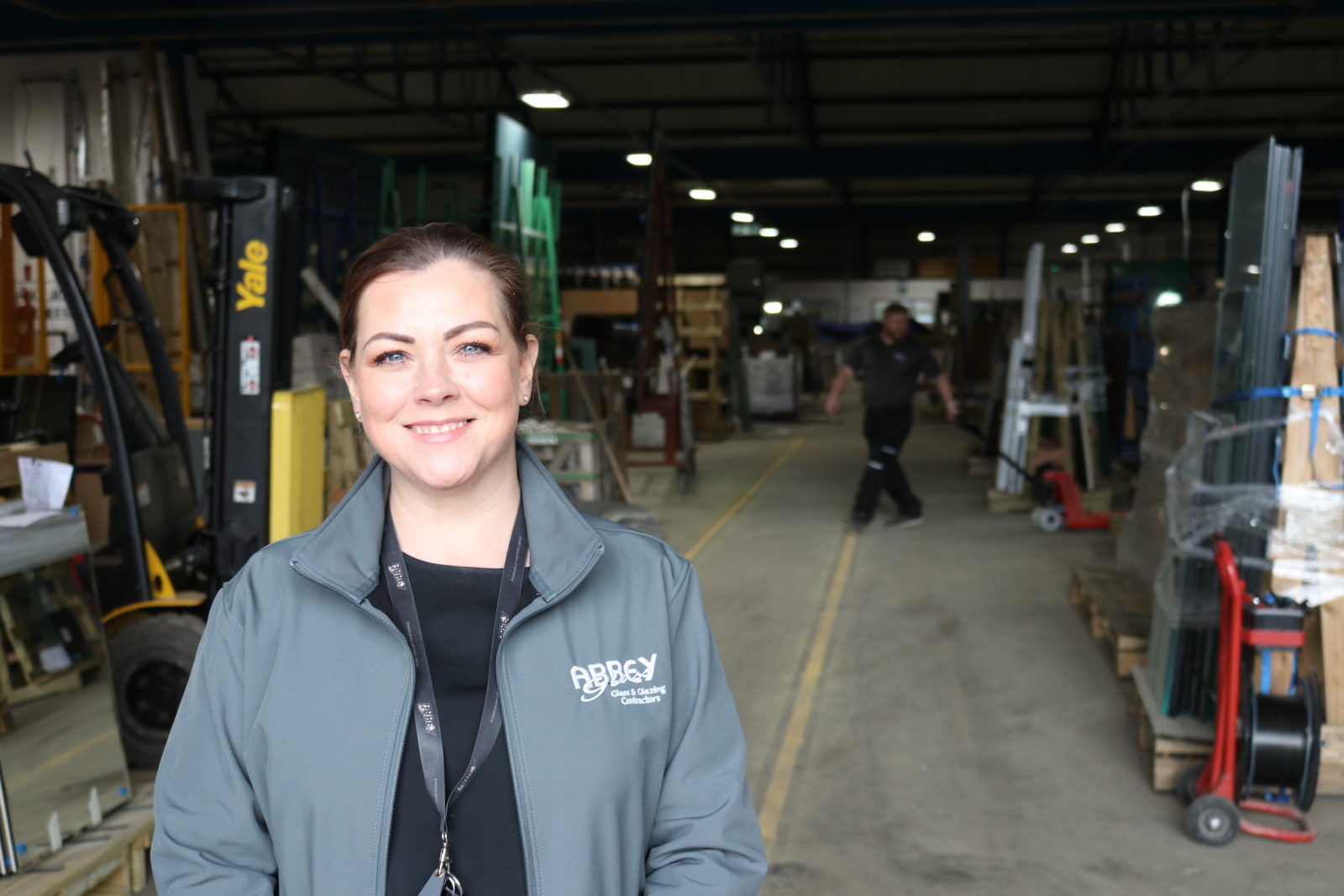
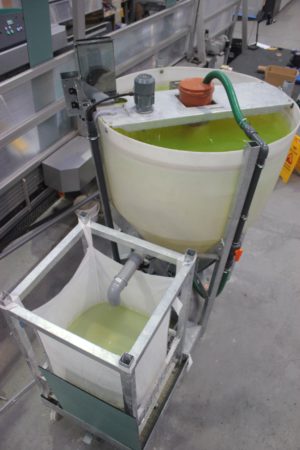
With wastewater and the carbon emissions generated in treating it, in focus, we find out how Abbey Glass is using Bohle’s sedimentor technology to lower energy usage, save money and drive an up-tick in product quality.
“Sustainability is becoming increasingly important for us,” says Angela Worgan, Abbey Glass. “It’s not only because we want to lower our impact on the environment. It’s also because our customers are now asking us for evidence to show what we’re doing in our business, to lower our carbon footprint and how we are progressing to net zero.”
Set up more than three-decades ago, Abbey Glass works with some of the UK’s leading retail, Hospitality and leisure brands, with Whitbread, Marriott Hotels, JD Wetherspoon, The Ivy, Easy Hotel and Point A Hotels on its ever growing client list.
It is the relationship with Whitbread, and particularly the Premier Inn brand, which was critical in driving Abbey Glass’ growth.
“Premier Inn by Whitbread is one of our biggest clients,” Angela continues. “They have an expectation that their suppliers are working to minimise their environemntal impact, their energy usage and their carbon footprint.
“There is a very clear expectation in hospitality and leisure that the sector wants to work with suppliers who are taking their commitment to the environment seriously, who can demonstrate what they’re doing and evidence improvements.”
Wastewater – an over-looked financial and environmental cost
Glass processors use water in large volumes, the treatment of which contributes to the 2.3 million tonnes carbon dioxide equivalents (MtCO2e) produced by the water industry in treatment of wastewater each year.
It also adds significant cost to production, either in the form of management or lower product quality because of contamination. This includes significantly reducing the lifespan of tooling and concretion of glass finings within the machine and tanks.
The cost of cleaning or changing coolant also quickly adds up. According to Bohle, using just 400 litres of water as part of your weekly cleaning cycle equates to a yearly water consumption of approx. 20,000 litres as well as high cost for its disposal.
“Some of our tanks can hold up to 3,000-litres,” continues Angela, “so it’s very important that we re-use and recycle as much of it as we can from an environmental perspective, but also an operational one.”
Better quality, lower energy costs and fewer emissions
The glass processing industry has traditionally relied on centrifugal water cleaning systems, however, according to Bohle, these can’t filter glass particles < 5 µm. This is something which, it argues, can over time, contribute to lower product quality and a build-up of concretion in the machine and its tanks.
It gets over this problem through an alternative system. Suitable for a wide assortment of grinding, drilling and sawing glass equipment, Bohle sedimentors use a sophisticated and automated, multi-stage process to remove contaminants from coolants and water. This includes filtering of glass particles of < 5 µm or less but doing so using far less energy.
Another key feature of Bohle’s range is that it uses a ‘bypass system’ for batch cleansing. This isolates water, coolant and flocculant, from the line during the cleaning process, completely eliminating the potential risk from flocculant contamination and tool damage.
In addition to giving glass processors as much as a day’s production back a week, improved product quality and increased service life of tooling Bohle says its range of sedimentors also trim around 10% off the costs of water disposal, paying back against purchase costs in as little as a year.
The view from the shop floor
Abbey Glass installed a Bohle Sedimentor 2.4 to its 12-spindle straight-line edger in summer 2022. Almost a year on, Richard Timson, facilities manager at Abbey Glass, said that product quality was up and water consumption significantly down.
“We wanted to lower our water consumption but also capture waste from processing, more effectively,” Richard explains.
“The Bohle Sedimentor 2.4 was a compact sized machine for our shop floor, which was important because space is fairly limited.
“The operation is extremely simple and you only use flocculant. The machine runs itself, you basically change the bag every week and that’s it.”
With its second sedimentor already on order, Abbey Glass is looking to add sedimentors to all of its glass processing and CNC lines.
Tax breaks to invest in sedimentor technologies
The Government unveiled its replacement for the super-deduction scheme in March’s budget.
The super-deduction scheme was launched by Chancellor Rishi Sunak on 1 April 2021 and allowed companies to access a capital allowance of 130% on qualifying plant and machinery investments.
Prior to this this, capital investments would either fall within a company’s annual investment allowance and produce relief of only £19,000 or alternatively be tax-relieved at 18% of the cost per annum.
At face value, the new scheme, which will run until March 2026, lowers the tax break by only allowing companies to deduct 100% of the cost (not the 130% under the super-deduction).
Given the increase in corporation tax from 19 to 25%, however, the value remains roughly the same at 25p per £1 of investment.
There are restrictions on what qualifies under the scheme but investments which make your business more efficient, for example sedimentors, are in practical terms easier to secure.
Closing thoughts
“In terms of the operation and how the machinery performs, we found that as well as lowering our operational costs and water usage, the quality of our edge work is also much better,” Angela continued.
“We’re also not having so much downtime to clean and do housekeeping so that means we can get more glass through our factory in less time, using less energy and delivering better quality for our customers.
“We’re seeing a commercial as well as an environmental benefit.”