Top quality
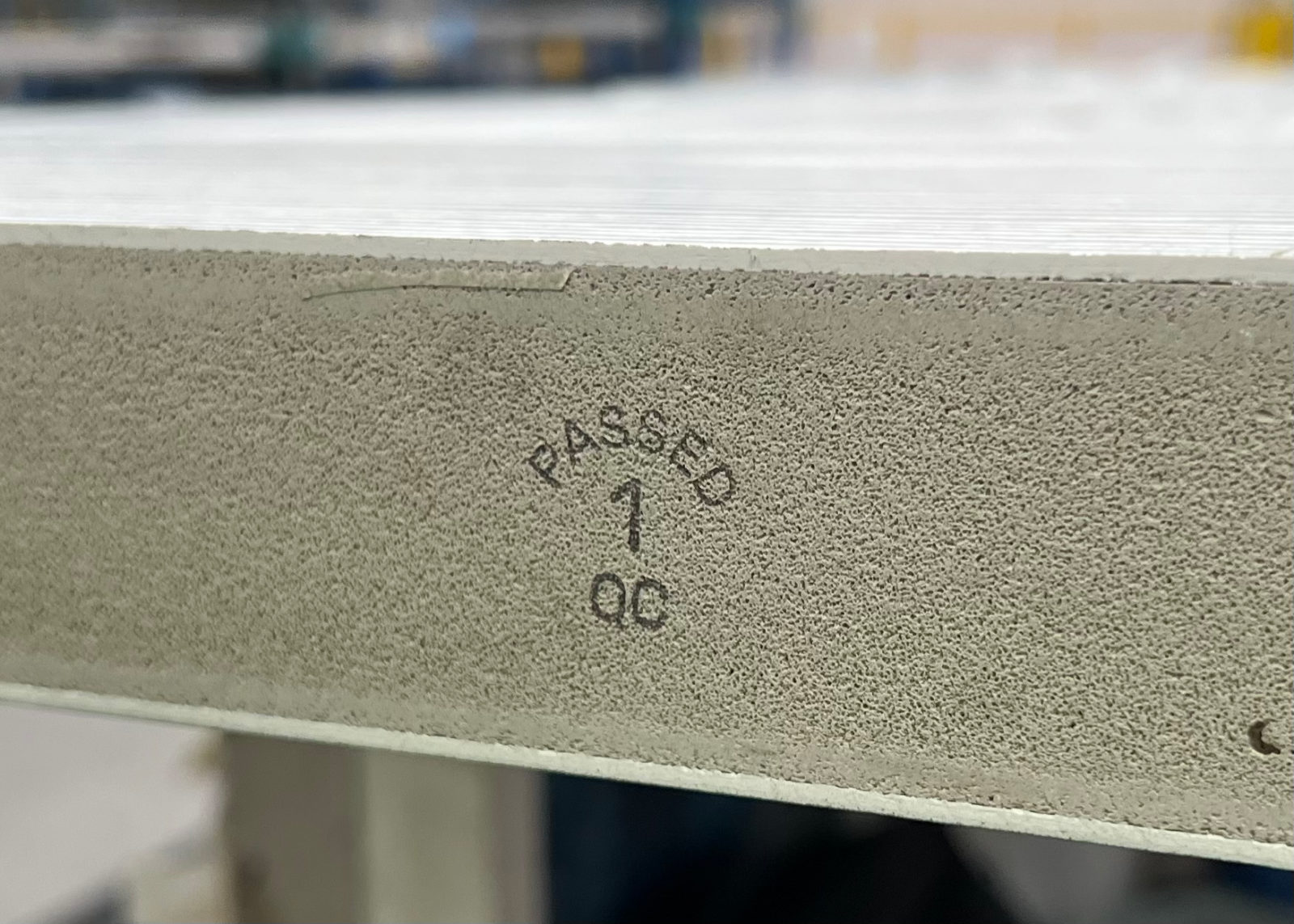
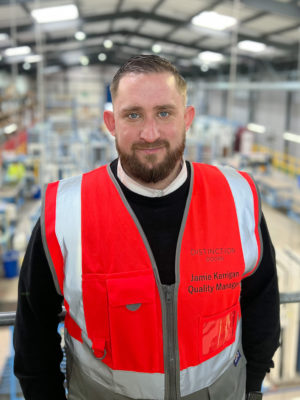
Glass Times meets Jamie Kerrigan, the man responsible for maintaining the company’s reputation as a supplier of premium, high-quality doors.
Maintaining Distinction Doors’ reputation for quality requires dedication and investment at every stage of the manufacturing process combined with the hard work and commitment of the company’s quality department.
Distinction’s associate director of quality, Jamie Kerrigan, leads all aspects of quality and continuous improvement. Jamie and his team of quality and improvement specialists are responsible for implementing and managing continuous improvement, and proactive, reactive, and legislative quality assurance throughout the business.
Passion for quality
Jamie joined Distinction in November last year, having previously worked his way up from quality assistant to SHEQ manager at Safestyle. With a passion for quality, Jamie’s first task was to prepare for the company’s ISO 9001 audit.
Within a handful of weeks Jamie introduced an improved quality management system which, following the independent audit, resulted in zero Nonconformance Reports (NCRs).
“I’d only been with the business a short time, so I had to just jump in with both feet,” comments Jamie. “This turned out to be for the best though – it was a great way to learn about the business and get a fair idea of areas for improvement.”
Cost of quality
And Jamie and his team were quick to act. Some immediate changes in Q1 2023 reduced the Cost of Quality (COQ) to the business to a world class rate.
“COQ depends on four key factors – prevention, appraisal, internal and external failure,” continues Jamie. “We began with a Failure Modes and Effects Analysis (FMEA). This is a systematic method which allows us to evaluate processes and identify points of failure. We then assess the potential impact of those failures, and this highlights the area/s most in need of change.”
They then created process controls using the FMEA data. “From this we developed process checks, test methods and minimum product standards which we trained our to staff in January.”
Quality control checks
One of these developments is the introduction of quality control stamps at every step of the manufacturing process.
Jamie has introduced three quality control areas. Each area is allocated a colour coded stamp dependent on their stage in the manufacturing operation – red for prep, green for paint, and black for glazing. Staff within these areas are tasked with conducting the final quality control inspection before the product is sent to the next process or despatch.
For added assurance, every quality inspector has a unique identification number. This number is for internal use only, but it enables Distinction to pinpoint exactly who conducted and passed each quality control inspection.
Employee engagement
Employee engagement is critical to the success of the quality team’s endeavours. “Quality assurance can require a change of culture,” continues Jamie. “Everyone takes pride in their work. This initiative encourages the operatives to take greater responsibility and care with the products they handle and produce.
“I am pleased that so far, the feedback has been extremely positive. Staff are happy with the accountability. So too are our customers. They are responding well to the improved process and like the visual reminder of our quality assurance.”
This measure is also driven by the operations managers and team leaders, as Jamie and his team turn their attention to quality improvement; what causes quality issues and how can they be corrected, prevented, and sustained moving forward. They are also using trend analysis to spot and stop specific issues.
“We’re in a continuous improvement cycle working to a ‘plan-do-check-act’ (PDCA) methodology,” concludes Jamie. “At the end of each period, we revaluate and set new goals to drive continuous improvement.”