A new era of manufacturing

Aaron Williamson, DoorCo’s new head of manufacturing, explains the processes he and his team are implementing to achieve best practice throughout the DoorCo manufacturing facility.
Lean and World Class Manufacturing (WCM) principles can mean lots of different things to different organisations and are sadly often misused or used superficially with no real understanding of substance.
With my background in the medical device industry and mission critical energy supply components, a true understanding of the power of lean is what has driven my first few months here at DoorCo, working with the team to restructure, establish and enhance processes to deliver a competitive advantage.
Building better
It’s no secret that DoorCo has experienced exponential growth over recent times and is now the UK’s largest composite door provider. Never shy to invest in people and equipment, from a manufacturing perspective, the business was approaching the ceiling in what it could do from a capacity perspective in its current set-up.
I was able to take a step back, review the space and the working processes, and grow capacity through strengthening the team and building plans to introduce the principles of WCM. Our ultimate aim is to adopt the 5S principles to achieve a clean, uncluttered environment, designed to decrease waste, optimise productivity through maintaining an orderly workplace and attain more consistent operational results.
This is only our starting place in our journey to achieving WCM; building the foundations to practically translate the 5S principles into reality through a clean and tidy workplace, with everything required for the job located where it should be. It sounds simple, but getting even these relatively basic steps wrong can have huge implications on productivity and quality.
Total restructure
As well as getting rid of everything we don’t need, and clearly labelling everything we do need, we have been working with Mark Towers, head of operations, to plan out a restructure that will see the shopfloor divided into three self-managing manufacturing cells with specific disciplines: standard doors, painted/stained doors, and glazing.
Taking a bird’s eye view of the manufacturing through-flow, it became obvious that the 31,000ft2 space could be used far more effectively. Historically, one big system was responsible for all doors and processes including glazing, painting and prepping, which often caused bottlenecks and delays. A door would also travel 250m round the factory – ¼ km – before it was ready. By adopting lean principles of removing the seven wastes – transportation, inventory, motion, waiting, overproduction, over-processing, defects – we have been able to reduce a door’s travel time to just 50m with the restructure. Not only does this indicate the advances we can make in opening up capacity, reduced transportation and motion also means less touch points for potential damage to the door, which will improve quality.
Lean principles also help to identify where further investment is needed in for example machinery, although it must be justified within the whole manufacturing ‘ecosystem’. As a result, we’ve brought in additional beam saws and also upgraded the significant extraction system.
People first
Of course, none of this would be possible without the right teams of people, a re-energised, can-do culture and shared values. As we take each step on the journey to WCM, people can see the improvements being made because they’re being listened to. They’re experiencing an improved work environment which creates a positive feedback cycle.
The three new areas of manufacturing each have dedicated teams, empowered to manage these lines effectively to ensure consistency. Within the teams there is a clear hierarchy and as part of the restructure we have been able to offer promotions into roles such as team leader.
This in turn signposts opportunities for other members of the workforce to grow within the business.
The culture of continuous improvement at DoorCo is what makes it unique, and everyone is integral. Ideas from across the manufacturing team have helped form our plan and we encourage any suggestions to help improve the business and service we deliver to our customers.
None of this is rocket science, but it does require consistency, tenacity and genuine teamwork, which fortunately are qualities seen throughout DoorCo. Why do we do it? Ultimately, to deliver consistently higher and higher levels of customer service, efficiencies to pass on to our customer through a value for money offering and to futureproof the business to keep ahead as we share and support our customers’ growth.
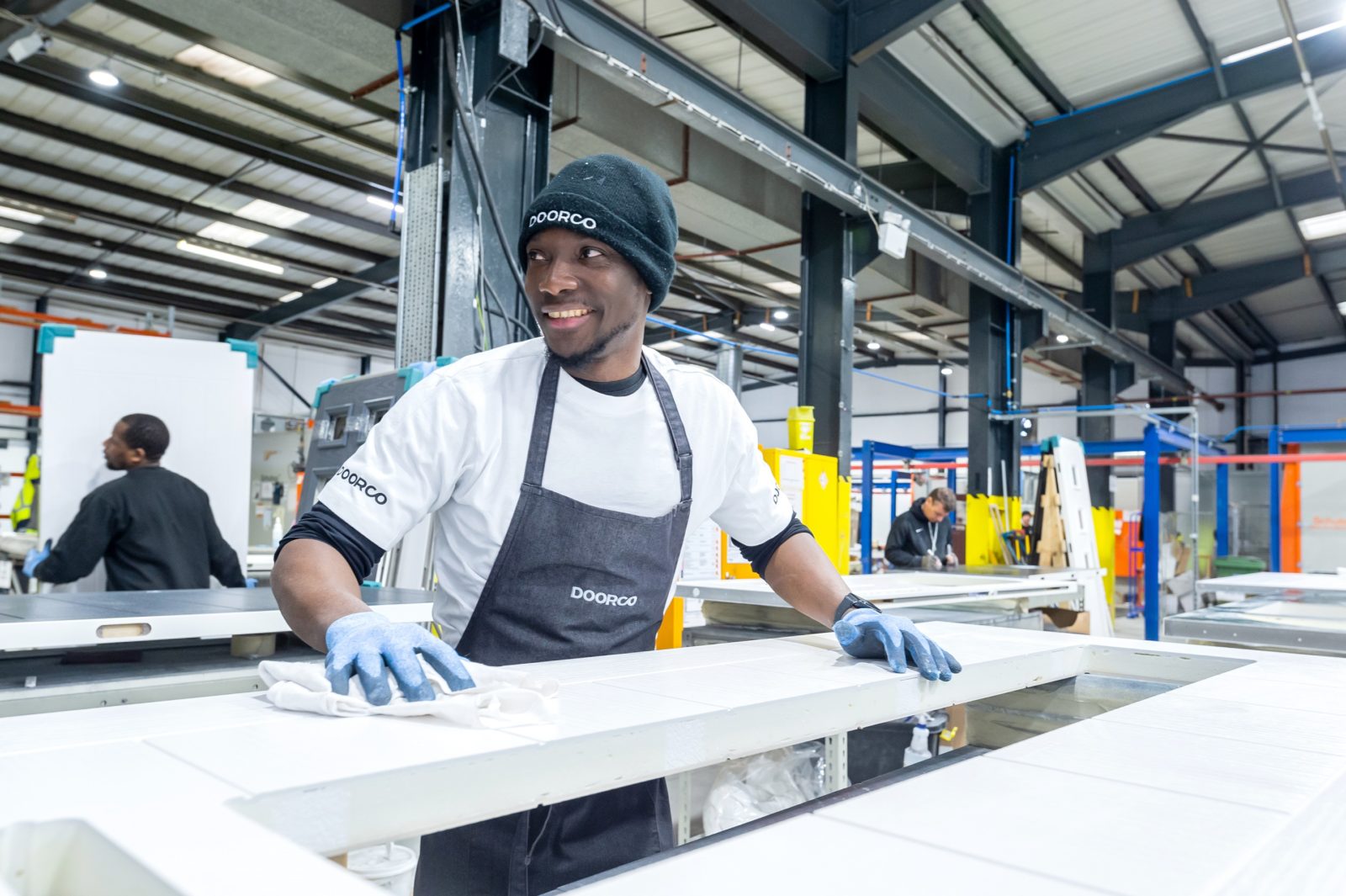