Sustainability and the circular economy
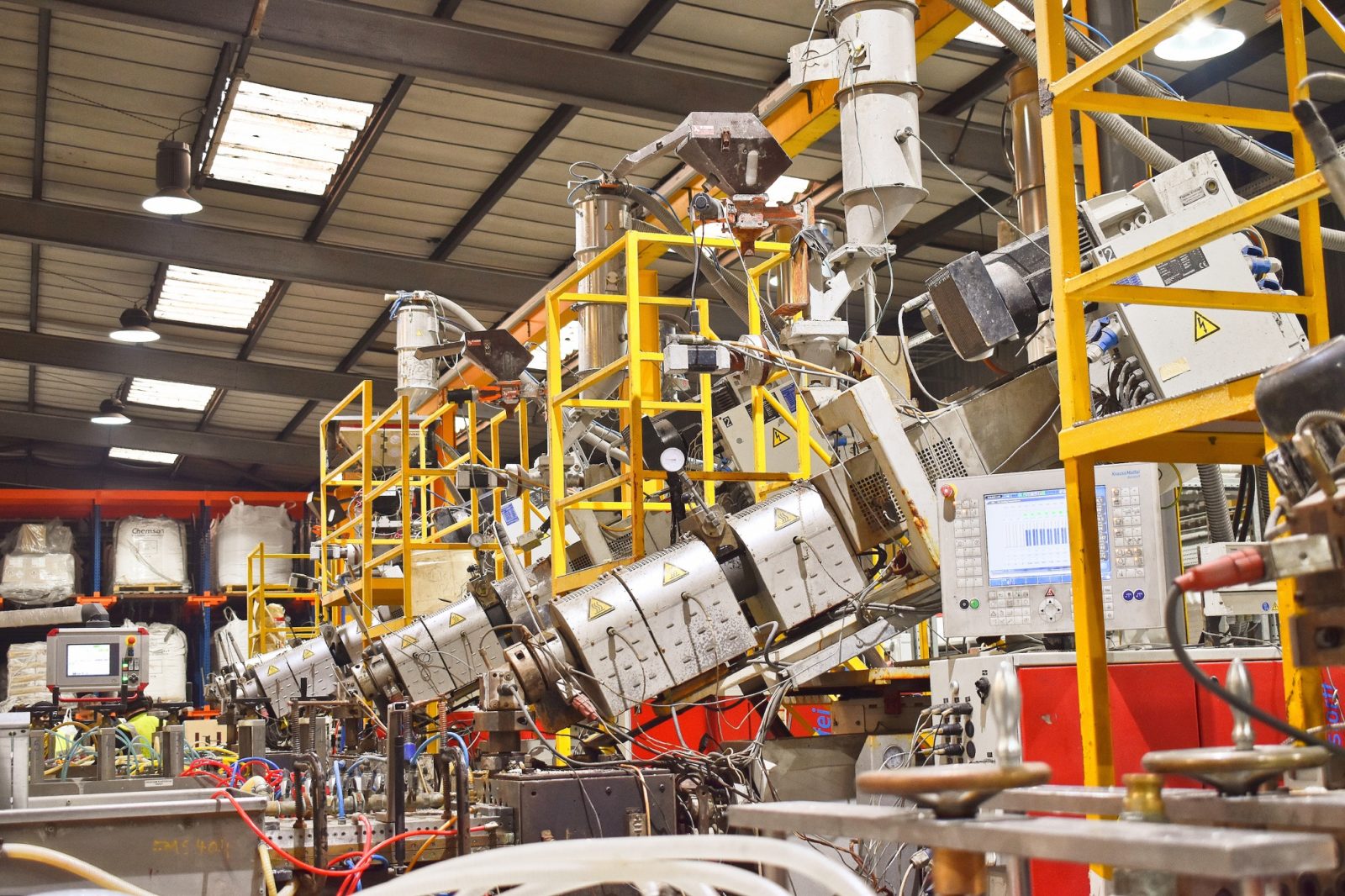
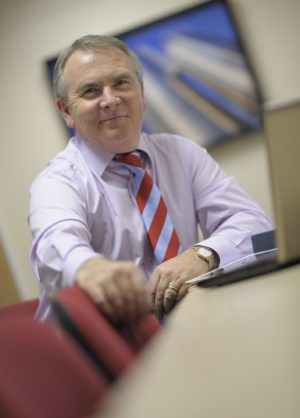
Colin St John, commercial director at Freefoam, argues that sustainability is not a trendy green label to be added to the same old products – it’s a completely different way of doing business and we all need to get on board.
The effects of climate change are increasingly hard to ignore, from devastating heat waves, droughts and forest fires to unprecedented hurricanes, flooding and sea level rises. According to analysis by NASA, 2022 was the fifth warmest year since 1880 (tying with 2015) and the last nine consecutive years have been the nine warmest on record.
It’s clear the Earth’s average surface temperature is rising. It’s clear we aren’t doing enough to limit those rises to below the 1.5°C to avoid the consequences set out in the Paris Agreement.
After a temporary dip in carbon emissions during the pandemic as factories shut and planes were grounded, CO₂ levels have rebounded and are growing again. Scientists expect global emissions will hit a new record of 37.5 billion tonnes for 2022. If this trajectory doesn’t change, the planet will warm to 1.5°C (above pre-industrial temperatures) in just nine years. A sobering forecast.
The key to solving this monumental challenge is surely to make real commitments to sustainability, as individuals and as businesses.
Pledges to be more sustainable must deliver real change though, as green badges or labels with no tangible benefits will soon be found out. There are swathes of new regulations in the offing to tackle ‘greenwashing’, effectively seeking to stamp out the practise of making claims about the environmental benefits of products which in reality fall short of their promise.
For manufacturers like Freefoam, sustainability can and should encompass many aspects of ‘going green’ – from reducing carbon emissions in production through continuous improvement, and reducing energy and material use by using a lean manufacturing ethos to switching to renewable energy generation to power manufacturing facilities.
All of the electricity used at Freefoam’s UK manufacturing site in Northampton, for example, is supplied from renewable resources.
Manufacturers also need to adopt the thinking and practices of the circular economy, which consider a product’s environmental impact from cradle to grave and act to make it less damaging to the Earth.
Reduce, reuse, recycle
In the past, manufacturing, Freefoam included, has followed a linear compartmentalised approach. We make a product, you use the product, and at the end of its working life, it’s thrown away. With the perspective of climate change, we can see that wasn’t the best approach, but now it’s just not sustainable. Future-fit organisations can no longer operate like that.
We, like many other manufacturers, are transitioning to a circular economy which enables the re-use and circulation of precious, finite resources such as PVC, to retain its economic value and eliminate waste. Our mantra at Freefoam is ;Reduce, Reuse, Recycle; and that is how we have set out to achieve a ‘closed loop’ product cycle.
Reduce – the first step is to do more with less and reduce waste during the manufacturing process. We do this through continuous improvements and investment in modern, efficient equipment to get products right first time – zero waste! Reducing post-production waste (PPW) is also important, and we’ve made improvements to get ours to under 5% across the group.
Reuse – PVC can be recycled up to eight times without loss of performance, depending on the application. We’re partnering with suppliers and improving our internal processes to develop superior material formulations which allow for high re-use rates of post-production waste (PPW) without compromising the quality of the finished product.
We use between 5% and 30% recycled PPW materials across our product portfolio including fascia, soffit trims, cladding, cladding trims, down pipes, woodgrain finishes, and mouldings.
Recycle – as well as recycling PPW into new products, we are looking for other ways to ensure nothing goes to waste. In the Northeast, we are trialling a project to ensure any unwanted or damaged products are returned to us for recycling, which could recover almost 30 tonnes of PVC a year. Any commercial waste we can’t recycle goes to Energy Recovery, where non-recyclable waste is burned at high temperatures to generate power for the National Grid.
Green credentials
To show customers they are the real deal and not ‘greenwashing’, manufacturers can aspire to attain certifications and memberships which prove their green credentials. For example, Freefoam has entered into a voluntary Climate Change agreement with the Environmental Agency to reduce our energy and CO2 emissions.
We have also agreed to meet stringent targets set by the British Plastics Federation. Accountability is essential in the quest for sustainability – you have to do what you say you are doing.
For several years, we have been ISO 14001 accredited; this is the internationally-agreed standard that sets out the requirements for an environmental management system. More recently, we became a founder member of Circuléire, a public-private partnership created to source, test, finance, and scale, circular manufacturing systems, supply chains and circular business models to deliver significant reductions in both CO2 emissions and waste.
A collective force for change
As a conscientious manufacturer, Freefoam is doing all we can to reduce our impact on the environment but we know that limiting or reversing the effects of world climate change isn’t achievable by just one organisation. We need to encourage everyone in the supply chain, including installers and suppliers, to do their bit and to do it now. If enough of us seek out opportunities in our working (and indeed our personal) lives to make a real difference, we can start to move the needle on sustainability in a positive way.