Leaders in glass
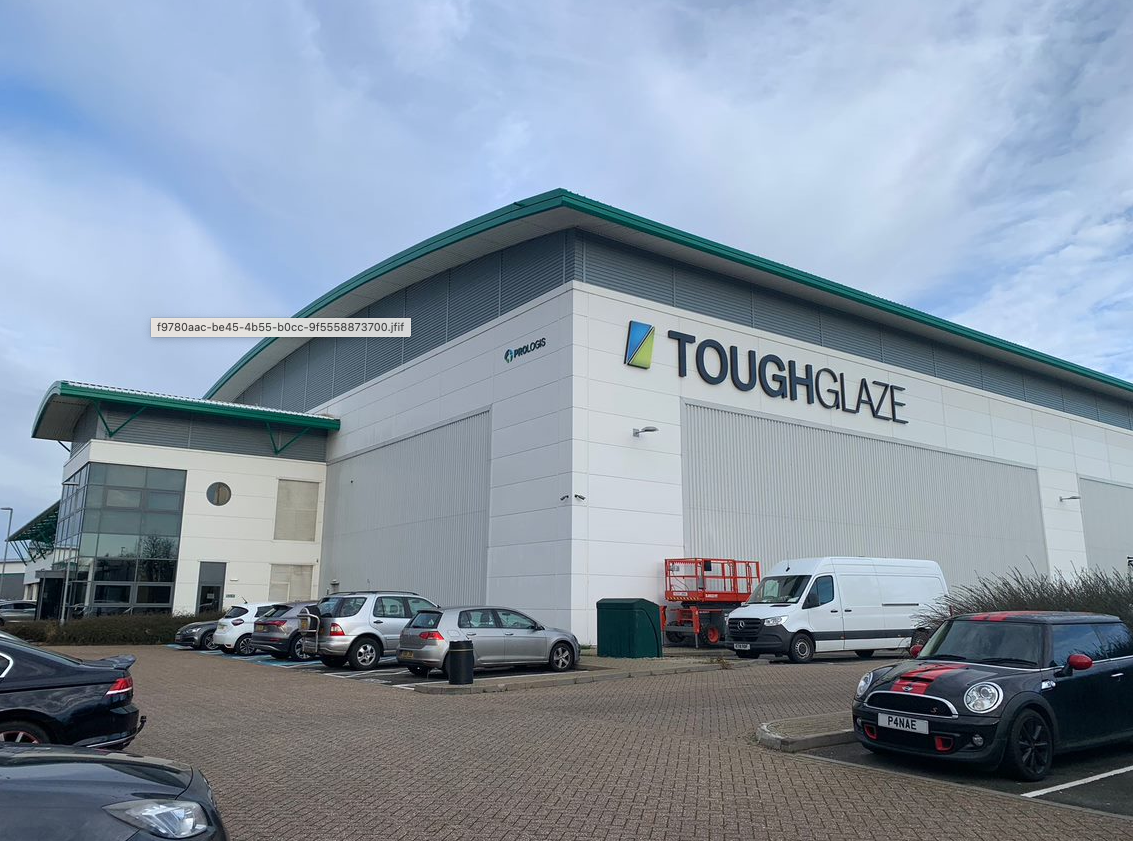
ToughGlaze, a family-owned glass processing specialist that’s fast approaching 30 years in business, has come a long way since it first opened its doors in Kingsbury, North West London. Now, with a new, state-of-the-art 100,000ft2 facility in Bedfordshire, the company has its sights firmly set on becoming the UK’s leading glass processor. Glass Times editor, Luke Wood, talks to Bhavik Varsani, managing director, to find out more.
When potential or existing customers visit our new facility here in Bedford, there’s always a big ‘wow’ moment when they walk through the doors and onto the factory floor,” says Bhavik Varsani, managing director of ToughGlaze.
“This is a multi-million pound investment for us, in machinery, processes and staff, but it’s one that’s enabled us to expand our reach geographically and to raise the bar in terms of the quality of our product offer and level of service.
“As a business we’re approaching our 30th anniversary, we’ve been in the industry a long time and we’ve always prided ourselves on being an industry leader,” he continues.
“But with the launch of our new Bedfordshire facility, it’s almost as if ToughGlaze has been re-born.
“We’re now bigger – and better – than ever, and we have the capacity to target significant growth going forward.”
Founded in 1993 by Vipul Vora, Ashok Varsani and Bharat Varsani, Toughglaze has come a long way.
The company was originally established at Rose House, a 3,000ft2 factory in Kingsbury, North West London, to better serve local sealed unit businesses with high quality toughened glass on shorter lead times – winning over customers who had, up until that point, ordered their glass from much further afield.
Its first toughening furnace was a huge investment and those early days were said to be a ‘hard graft’ for ToughGlaze’s founders, who worked seven days a week, often late into the night to process orders, cut, arris, toughen and then deliver the glass.
However, the passion and commitment from Ashok, Bharat and Vipul laid the path for ToughGlaze’s future, relocating to larger production facilities in North West London and then on to the current Bedford HQ in 2020 – a move that happened to coincide with ‘peak’ Pandemic.
“Setting up a new factory of this size would have been a big operation at the best of times, but during Covid it really was a massive undertaking,” explains Bhavik. “For starters, we couldn’t get any hotel rooms for the engineers, so we had to rent temporary accommodation so they could stay on site.
“As soon as we managed to get up and running there was a glass shortage, which was then followed by the fallout from Brexit so we struggled to find drivers – then we had the war in Ukraine and the impact on energy prices…the last few years have been incredibly challenging, but we are now in a place where we can really start to move forward,” he continues.
“A big part of that is because we have invested heavily in automation, as well as new software, and we’ve taken advantage of a much larger factory to optimise the flow of production so we are now operating much more efficiently. That has allowed us to double our output, while still only running at 50% overall capacity.
“Our new location has also allowed us to establish a much bigger presence nationally, which has allowed us to win high profile projects up and down the country and in some cases, overseas.
“In addition, we’ve also taken the opportunity to bring in new people, to revitalise our work force,” he adds. “Finding skilled people is obviously another big ongoing challenge for the industry at the moment, but again, it’s something we have successfully managed to overcome and we now have 149 employees here at Bedford, including a dedicated team of delivery drivers to support our growing nationwide customer base.”
Sustainable quality
With ISO 9001.2015 accreditation, the globally recognised quality management system standard, the team at ToughGlaze has also invested significantly in sustainable operations.
That includes an advanced water treatment system that recycles up to 26,000 litres of water a day, and an initiative that means all waste glass is returned to Guardian to be recycled as cullet, a service that ToughGlaze can also extend to its customers who don’t have the capacity to recycle their own waste product.
A scheme is also in place for plastic recycling and the company has introduced multiple charging points for electric vehicles. Heat from the toughening plant is also repurposed to heat the factory during the colder months.
“We are well placed to service any increase in demand for low carbon products or for projects where sustainability is a key factor,” says Bhavik.
“We offer a wide range of glass, including large volumes of 4mm to IGU manufacturers, alongside more specialist fire resistant, acoustic, structural, decorative, heat strengthened and laminate product, and for a broad range of applications and sectors.
“Demand remains strong for higher value, specialist glass and we’ve also experienced a big upturn in interest for our switchable glass offer,” continues Bhavik.
“It’s a really exciting product, the result of a strategic partnership with the most advanced LCD engineering laboratory in the world, and it features a third generation NPRLC film.
“It has lots of applications, from high end residential where it can be specified for bi-fold or sliding doors, shower screens or walk-on panels, through to commercial, healthcare and hospitality projects as well as for buildings where security is a priority, such as prisons or airports.
“We’ve also joined forces with a leading UK manufacturer to supply our switchable glass, an arrangement that came about partly due to the inherent quality of the product, but also because we were prepared to invest a lot of time and effort to fine tune the offer to suit our customer’s requirements,” adds Bhavik.
“When ToughGlaze first started out at Rose House all those years ago, a key production benchmark was 300m of toughened a day. We are now producing far in excess of that, but the underlying principles of quality and service remain.
“Our goal now is to be the UK’s leading glass processor,” he concludes.
“Whether the industry sees a rise in demand for triple glazing, or for laminate, in response to new regulations coming down the line, or whether we see even more interest in our specialist product ranges – we are ready, and every month we are pushing to raise our standards even higher.”
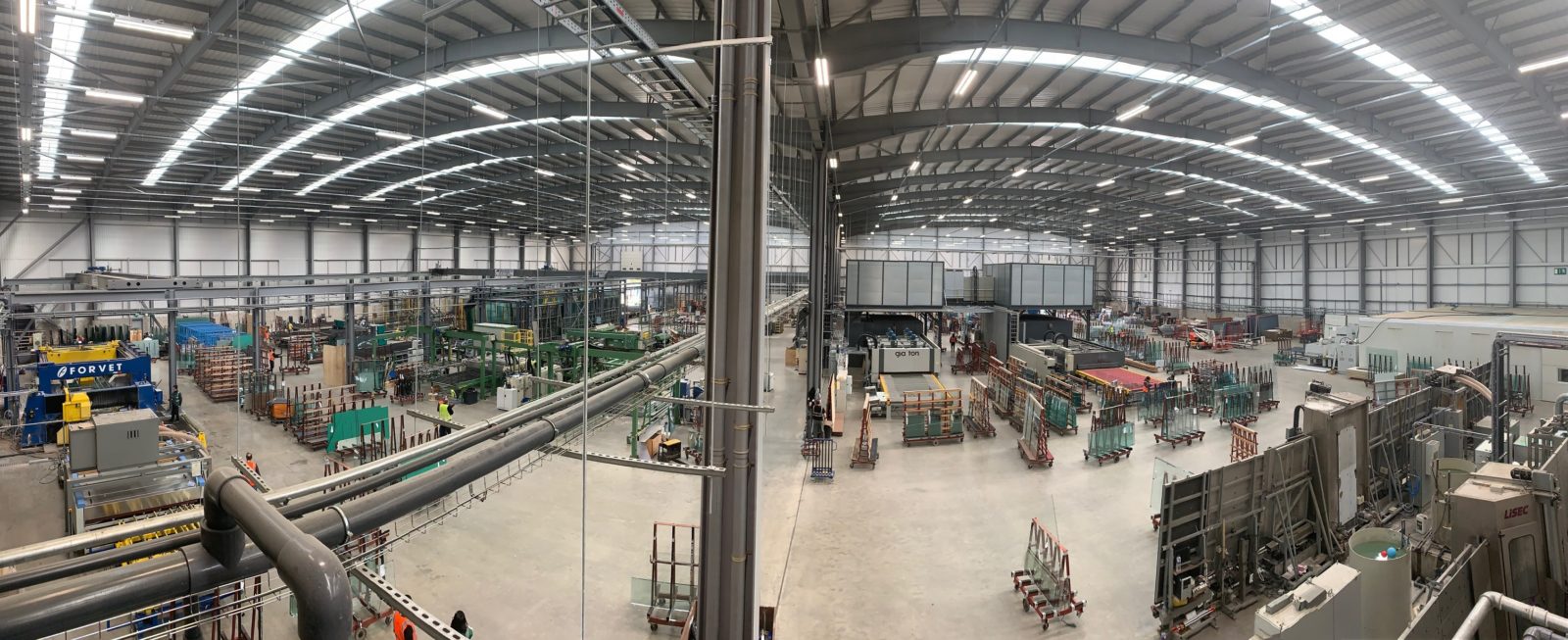