Demand prompts move
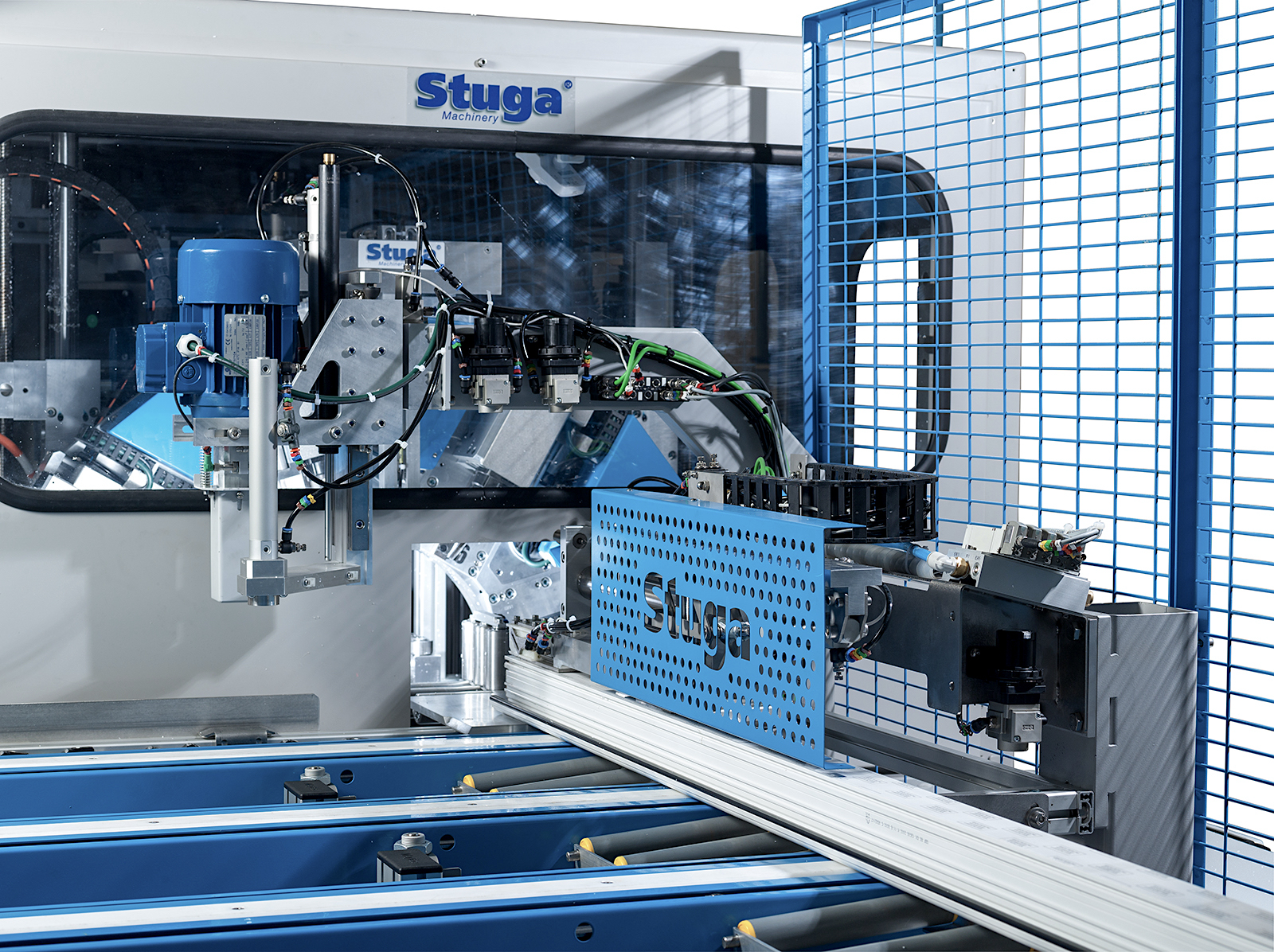
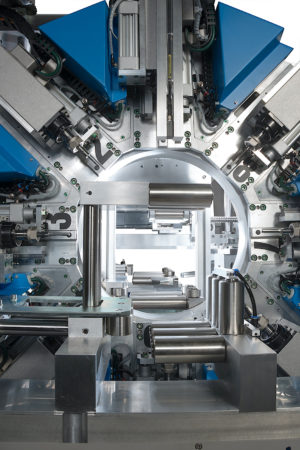
Stuga Machinery has moved to larger premises in Great Yarmouth in response to increased demand for its machining centres.
Joint owner Steve Haines said the move is part of a bigger plan to create flexibility so that the company can continue to develop new products, reduce lead times, and strengthen it service department.
“The new factory is 30,000ft2,” Steve told Glass Times. “Not only is that twice the space we had originally, all of that is one uninterrupted area. Before, we had three units side by side, with two dividing walls that needed to be accommodated.
“We also have two overhead cranes that allow us to be more flexible with the flow of product through the factory, as different modules can now be easily moved as and when they are required.”
Steve explained that Stuga is traditionally cautious about expanding to meet what often turns out to be temporary fluctuations in demand. The supply of machines, he said, should be viewed over years, not months, because a downturn in the economy can have a significant impact on the order book. It is far better to expand and contract more gracefully.
However, the pandemic has resulted in a significant and, seemingly, sustained demand, and the company exceeded its 2020-21 budget, even though the factory was offline for six weeks at the start of the financial year.
Therefore, we had to do something because our order book has grown exponentially,” Steve said. “We can’t believe how busy it is out there, and we have customers who only want a Stuga machine.”
With delivery times already pushed out to 2022, Steve said the plan was to speed up production and, essentially, make more machines.
“Over the next year, we hope to get a 20% increase in production,” Steve said. “That’s a bit of a finger-in-the-air figure, but we need to take into account the time to settle in and the fact we’ll discover new efficiencies.”
Part of the move to new premises is to improve the machines, and the pandemic has had a surprising effect on the research and development team.
“We have a designer in Middlesbrough, with whom all contact is conducted through Zoom, Steve said. “We would never have entertained the idea before 2020, but we can have our research engineers all over the place, working on idea, and regularly discussing developments over the internet. It means we can employ the very best talent the industry has to offer, without worrying about relocating people.”
The move to larger premises is also benefiting the service and spare parts division.
“We have well over 200 automatic sawing and machining centres, as well as another 120 stand-alone saws and prepping centres in the market place, and all of them need servicing,” Steve said. “There are some that cannot be easily upgraded, and so we have designed workarounds to overcome their potential obsolescence.
“Customers simply don’t want to let go of old Stuga machines once they have them, even if they only provide a back-up when newer machinery is faced with maintenance downtime.
“This has all created a significant amount of work, and is essentially a bit of a safety net if demand were to crash like it did in 2008; we can use space at the factory to rebuild and upgrade machines if demand for new machines drop of a cliff.”
The company is now on a recruitment drive, and is willing to train up the next generation of engineers, or retrain those who have worked in another industry.