Are you ready for flush windows with sub-0.8 U-value?
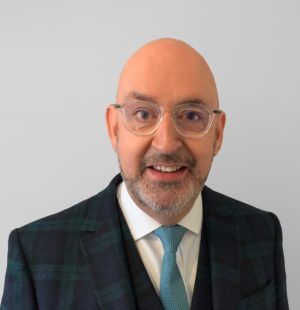
By Ian Cocken, Aluplast’s director of sales and marketing.
The drive towards better thermal performance, greater choice over style and colour, improved security, and a more secure supply chain has put a brighter spotlight on systems companies than ever before, says Ian Cocken, director of sales and marketing at Aluplast.
“If the last three years have taught us anything, it is that some systems companies operating in the UK struggled with the extra demands placed on their business models,” he says. “In the months after lockdown, we picked up a lot of new fabricator customers who had found their supplies come to a halt, especially if they were ordering specials such as colour and flush.”
Cocken points out that while we are unlikely to experience the supply chain pressures that were present during 2020 and 2021, the fallout proves that suppliers need to be one step ahead of demand.
“The reason why we were a port in a storm two years ago is because we had already invested in those areas that were popular, such as colour and flush windows,” he says. “And we continue to invest in new products to meet future demand.”
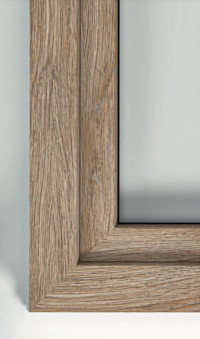
Thermal performance will be the next battleground, Cocken adds. With many systems reaching the limits of their capabilities, even with triple glazing, weaknesses will be exposed as the U-values of building components come under greater scrutiny.
“The government is targeting the built environment in its bid to meet its net zero target by 2050,” Cocken says. “As a result, we expect to see the introduction of the Future Homes Standard in 2025, which could see U-values for windows and doors with >60% glazed area going into new properties drop to 0.8W/m2K.
“This proposed increase in thermal performance is steeper than we’ve seen with previous regulatory updates, and it’s going to put a strain on window design, especially if systems companies are hoping to simply update existing products.”
Aluplast has gone back to the drawing board for Ideal Neo, which it unveiled last year. The new flush-fit, 76mm front-to-back system is now available in the UK, and according to Cocken, offers significant opportunities for fabricators and installers.
“On a headline level, windows manufactured using Ideal neo can achieve U-values as low as 0.73W/m2K,” he says. “But the key advantage for fabricators investing in this technology now is that the frame design allows U-values to be pushed much lower without significantly changing the overall design of the window – they will be effectively future-proofing themselves against further regulatory updates.”
Ideal Neo offers a base-level 1.2W/m2K Uf-value, and the ability to carry units up to 51mm. This means triple glazing can easily be incorporated, which presents the opportunity to offer windows with ultra-low U-values.
Further options contribute to Ideal Neo’s energy efficiency. These include ‘powerdur’, a specially designed co-extruded fibre-glass reinforcement, which improves the thermal performance and makes the windows 20% lighter than conventional windows. This saves fuel during transportation, relieving strain on the environment in the process.
Glass units can be bonded to the frame, which improves weather tightness, thermal performance, and the window’s rigidity. And since Ideal Neo windows are lighter, glass bonding doesn’t impact on the weight during installation.
The Ideal Neo system also has a classic centre seal – ‘safetec inside’ – which is a special, extruded middle rebate with a third internal seal. This ensures better tightness of the entire construction, improves thermal and acoustic properties, and makes it more difficult to force open the sash by blocking access from an external attack.
Finally, all profile supplied by Aluplast, including in the UK, is made from Ecotech, which maximises the amount of recycled content in a profile’s design.
And all profile is available in 40 different foiled finishes, including Woodec and Aludec. These are next generation foils that accurately replicate timber and aluminium and open up opportunities for fabricators and installers targeting high-end installations.
“We know what challenges are coming, so we’ve invested accordingly,” Cocken says. “Those fabricators who do the same will also be prepared.”