Stuga targeting ambitious goals
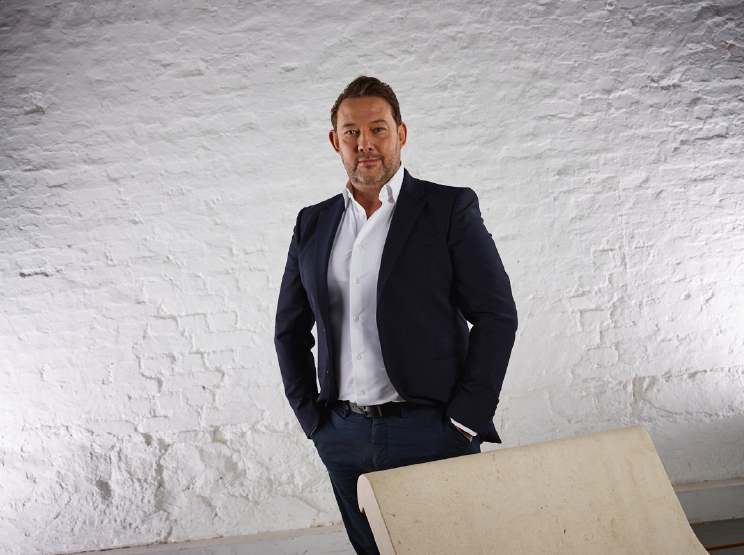
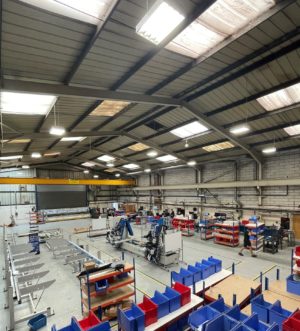
Since the acquisition of Stuga Machinery in 2022, the Great Yarmouth based manufacturer of CNC sawing and machining centres has made several key appointments in recent months, in addition to restructuring and reorganising its factory space.
As a result of the growth in Q4 of 2022 and Q1 of 2023, it has made further investment in people, adding Mark Laithwaite to the sales team to cover the North of England and NI; Craig Savage to lead a revamped service function – bringing increased focus on operational development, performance and customer satisfaction – as well as John Ward, who joins Stuga in a new role as project manager.
Ed Williams, Stuga’s managing director, commented: “With a strong and diversly skilled team now in place, we have shifted our focus and efforts to business development initiatives that improve our performance and continue building on our capability, thus ensuring service received by our customers is truly world class.”
Service
On his new role, Craig Savage explained: “Our customers have always benefited from our industry leading after-sales service, ensuring they get the most out of their Stuga sawing and machining centres, but as we grew (and continue to grow) the sales of Stürtz welding and cleaning machines, we had to develop the skills of the team and the operational muscle to deliver an equal or better level of service on these products too.”
The addition of new heads into stock control and order management have improved Stuga’s ability to handle increased spare parts sales, especially since Stürtz already has an install base of over 100 machines in the UK market that – in most cases – Stuga can now provide after-sales support on.
Developing excellence
According to Ed Williams, the addition of new personnel has proved to be a major success, with Stuga having secured significant investments in several fully automated welding and cleaning lines, including a range of inline and vertical welders as well as corner cleaners.
“The management team has worked really hard with all members of staff over the past six months to develop their individual roles and collective responsibilities, the processes and procedures they work with – and all this while carrying out their day to day tasks,” he said. “The Stuga and Stürtz relationship is seen as something of a sleeping giant by the industry and I am thrilled to say that we’re dealing with the growth incredibly well.”
Project management focus
John Ward is Stuga’s latest hire and will be responsible for implementing strict project methodologies and overseeing the progress of all machines; from sales through to final sign-off.
With 30 years’ experience in the management of complex capital machinery projects, John is said to be well equipped to handle what is evidently a crucial role for Stuga and with a high degree of capability in the implementation and development of best practice for project services.
John commented: “In a business that is growing sales of an increasingly diverse portfolio of machines and services, it is vital that Stuga has a function that provides a link between all the departments of the business. Project management is the glue that binds it all together really and I am excited to be part of the team.”
An environment for success
Having the right people and the right processes in place is vital but for this to adhere requires an appropriate and ‘fit for purpose’ working environment.
“This was the most challenging part for us,” said Daniel Goodrum, production manager at Stuga since the beginning of the year.
“Trying to re-design a completely new layout to the factory has not just taken time to finalise but was also a challenge to implement at a time when our production area is full of customer machines.
“In the past, we found it difficult to just down tools for a few weeks to carry out this sort of work, but with the support of the leadership team and the freedom to make critical decisions, it worked out really well.”
By embracing change and remaining adaptable, Stuga is now poised to make significant strides forward in pursuit of its ambitious goals. “Working on multi-million pound turnover projects can be daunting for many – it’s a big deal of course – but we’re developing a culture of confidence and empowering our team with the skill and support to make good decisions,” concluded Williams.
“Everyone is excited to see what lies ahead and is committed to making the most of this exciting new journey.”