Shaping a responsible future
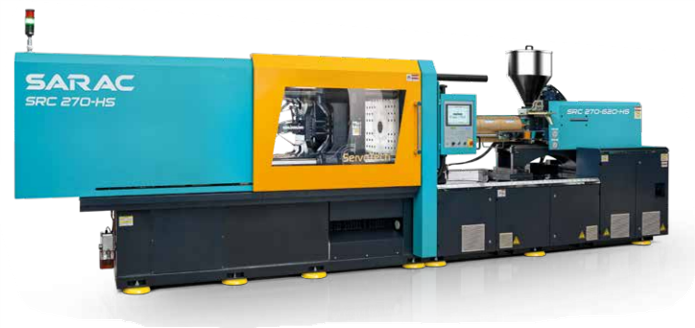
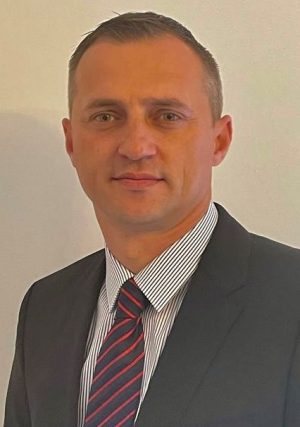
Ned Kenjic, operations director at Yale, discusses Assa Abloy and Yale’s ongoing sustainability efforts.
The Yale brand has a history of innovation going back hundreds of years. However, we also have a strong sense of responsibility to the environment we operate in – and that means maintaining a UK manufacturing base that not only produces high-quality products, but helps to shape a responsible future for generations to come.
As part of the Assa Abloy Group, sustainability is integrated into everything we do. The group has a long-term, science-based commitment to a sustainable future, with targets such as halving our scope 1 and 2 greenhouse gas emissions by 2030 and achieving net-zero no later than 2050.
Last year, our efforts led to some great results. These included decreasing our water intensity by 18%, our energy intensity by 12% and our carbon footprint by 4% – all significant strides in mitigating our environmental impact as a company.
We also carried out 765 sustainability audits of direct material suppliers and achieved 246 verified and published Environmental Product Declarations (EPDs). A complete mapping of a product’s environmental footprint based on a detailed Lifecycle Assessment (LCA), an EPD allows customers to make an informed decision when selecting a solution.
Leaving single-use plastic behind
Another important Assa Abloy target is to remove all single-use plastic from our business by the end of this year, helping to mitigate pollution, protect wildlife and preserve the health of ecosystems for generations to come.
At Yale, we’re playing our part in this by recycling the in-house polypropylene materials at our Centre of Excellence for Door Products in Willenhall, which equate to around 30% of our material consumption.
The factory currently has eight plastic injection moulding machines, which are used to produce useful components such as profile packers, one-piece keep end caps and dust tidies.
Thanks to investments in new machinery, we are now able to separate the sprues from the components, granulate the sprues and reuse them in the plastic moulding process. This drastically reduces our dependence on virgin plastic materials, resulting in 27,000kg less plastic waste per annum.
Additionally, the reuse of granulated sprues in the plastic moulding process lowers our need to purchase new plastic material. This again helps the environment as it will discourage the manufacturing of plastic in the first place.
While it’s important to celebrate successes like these, this is no time to rest on our laurels. As an industry and as a planet, we still have much to do before we are on the right track. That’s why we will continue to strive to set the standard for sustainable practices within our industry, helping to pave the way towards a greener future.
To find out more about Yale’s sustainability policy and download Assa Abloy’s new Sustainability Report for 2023, visit www.yaledws.co.uk/uk/en/about-us/sustainability.