Never neglect your CNC
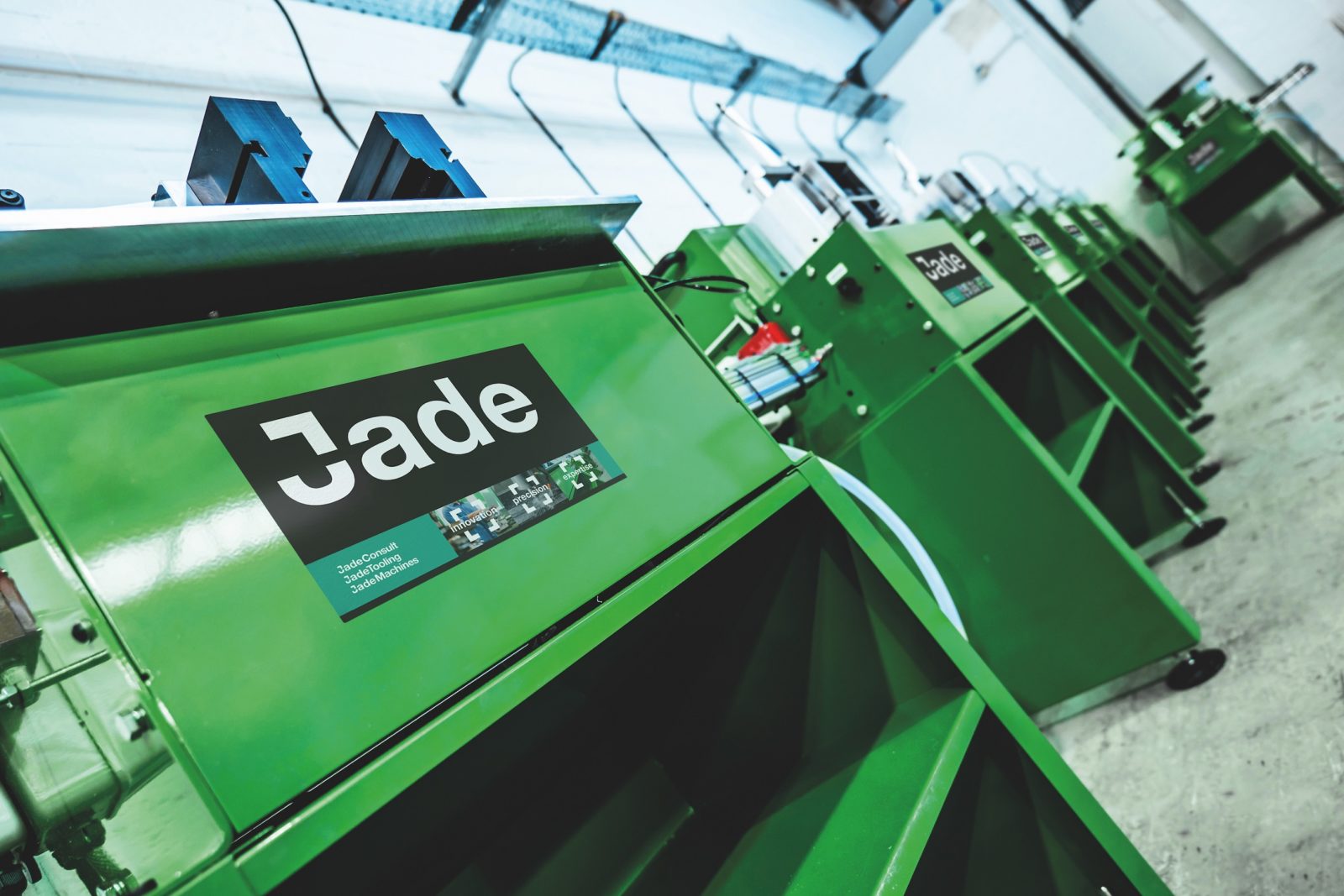
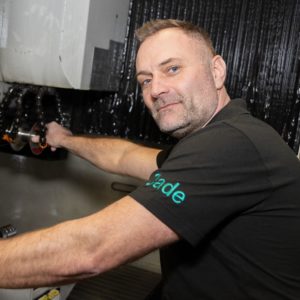
Jade Engineering’s Adam Jones knows a thing about CNCs – his firm makes the tools for most of them. But, he says, too many CNCs are taken for granted.
CNC – ‘Computerised Numerical Control’ for the uninitiated – controlled frame production machines have been with us for around four decades.
It is fair to assume that the majority of window and door frame manufacturers will have at least one such bit of kit performing hundreds of repeated operations, usually with the minimum of downtime, efficiently and accurately.
The concept of a CNC machine doing the work of perhaps four or five people, is at the core of the popularity of this type of equipment. When they first gained popularity in the window and door industry of the nineties, they were heralded as a solution to the labour shortage. Consistent quality and efficiency are also, of course, crucial.
However, familiarity with CNCs has also bred a degree of contempt, according to one frame manufacturing expert.
Adam Jones, who with Sean Mackey heads up Jade Engineering, which supplies tooling for almost every UK frame-making CNC in operation, says that he is surprised at how many factory owners – having spent thousands of pounds on such complex machines – fail to impose a planned maintenance programme, beyond what the supplier might include in the capital cost of the equipment.
“When the kit is first installed there is usually a flurry of excitement on the shop floor and around the board table about what the new machine can do for the company, and that is usually justified,” says Adam. “The technology powering even quite humble machines these days is extraordinary and at the top end, the functionality, precision and output is amazing. But ultimately, they are machines, they have a job and of course, they are quickly taken for granted.”
When the honeymoon is over, believes Adam, corners are often cut, in the maintenance of the machinery, rather than just frames: “No matter how clever these machines are, if the blades and cutters and heads are not kept sharp then problems will occur,” he says.
“In addition to product quality suffering, damage is being done to the moving parts of the machines. Worn tools set up imperceptible vibrations that increase wear on bearings, spindles and other components and eventually something expensive will break – plus the cost of lost production of course.”
Over the past couple of years particularly, says Adam, most fabricators have been running at full capacity, an issue that may result in oversights: “When delivery deadlines are being stretched, there is an obvious reluctance to take a machine out for servicing. And even though changing tools can take just a few minutes, many are only changed when product quality begins to visibly suffer.
“This can be resolved by imposing a planned tool change and maintenance programme,” he continues.
“If it is anticipated that a machine will be out of service for a day or two depending upon the maintenance required, then arrangements can be made to alleviate any potential disruption. That sounds obvious, right? So why are there so many factory owners out there prepared to wing it? It is far more disruptive to fix a broken machine than service one. And tool changes take minutes.”
Of course, the cynic may argue that scheduled tool changes, rather than running a finger along the edge of a blade, benefit Jade Engineering as well as the fabricator. But, adds Adam, even the cost of the tools may be mitigated, as his firm has introduced a sharpening service: “An operation producing around 400 frames a week should change tools every six months or so and other numbers, pro rata. That is a fact of frame-making life.
“We get that machine tools are one of the highest overheads of the frame making process. But to ensure optimum output and product quality, the tools need to be sharp.
“We understand that there is immense pressure on overheads, especially energy, and that every area of cost must be examined. That is why we now offer a regrind service that extends life of tools by a factor of three, whilst slashing costs by 75%! And a box of tools can be returned to us for as little as a tenner.”
Planned maintenance, including tool changes, benefits everyone, concludes Adam: “It helps to keep our own CNCs running at peak efficiency too, and we can plan our own maintenance cycles.”