How to cut waste and save money
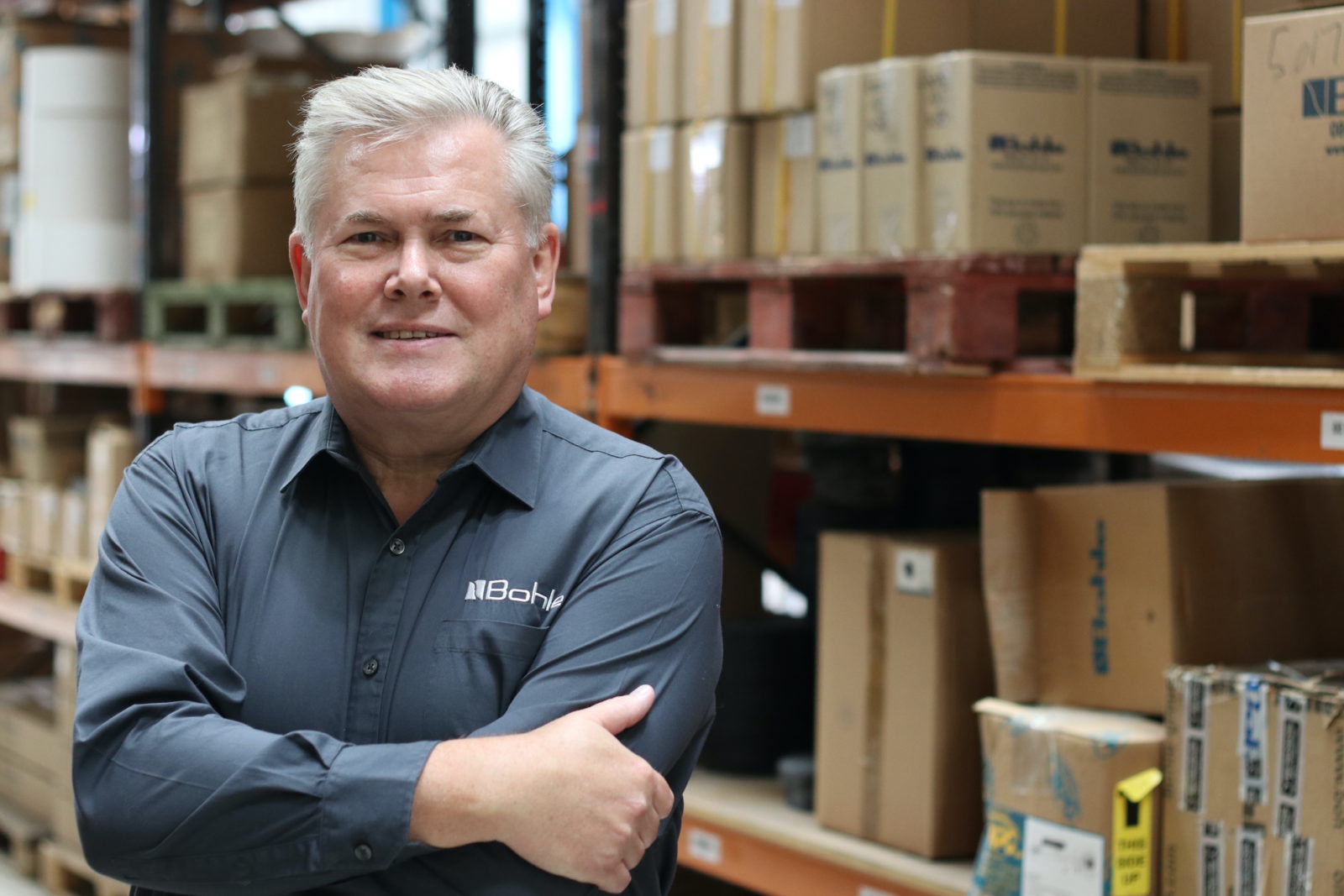
By Dave Broxton, MD, Bohle
As the market contracts, and the cost inputs rise, all business supplying the construction industry and home improvement sectors must work harder to build margin into their processes.
This, argues Dave Broxton, MD at Bohle, will be a defining feature of 2023, and will require more efficient ways of working, even as price rises are passed on to the end user.
“We’re all paying more for our energy, we’re all paying more for our fuel, our carriers are charging us more to deliver goods, the float lines are facing enormous increases in the price of gas – and that clearly has to filter through to the end consumer,” Dave says. “And I don’t see that changing during 2023.”
Maintaining margin
For many glass processing companies, one of the biggest overheads is typically the cost of the float glass, and during 2022, this cost was at the mercy of volatile price fluctuations. Price rises were often frequent, as were surcharges, which could vary from glass manufacturer to glass manufacturer, and could often catch companies out if they weren’t passing it on through the supply chain.
Dave believes this situation is unlikely to change in the short term, and that reducing waste and investing in the right equipment is the key to maintaining margin as a glass processor.
“The right optimisation software can help you use glass efficiently, but what we need to do more than anything is cut the wastage of such an energy-intensive material,” Dave says. “Needlessly throwing glass cullet away is unforgiveable.”
Preventing glass wastage starts as soon as the cutting wheel makes contact with the glass on the cutting table, and getting the right system in place will ease pressure on your glass supplies, Dave argues.
“Within our Silberschnitt system, we have a cutting wheel and cutting fluids for any type of glass, plus we can give free expert professional advice to people who are cutting large volumes of glass to reduce wastage,” Dave says.
“It’s difficult to put a percentage on the savings that can be made by using the right wheel, with the optimum cutting angle and the right fluid, but we believe that we can make incremental savings which will add up over the course of a year.
“You can go into any glass plant in the UK, and look at the edge quality of the glass before processing, you will find shelling and chips – little things that require additional processing time but can be ironed out by using the appropriate wheel, cutting fluid and the applicable cutting pressure.”
Stress-free
Choosing the right cutting fluid is essential for cutting glass efficiently: cutting fluid lubricates the cutting wheel, which provides smoother cutting, and it also maintains the stresses within the cut, offering better break-out performance and more stable edges.
“Cutting fluid stores those stresses within the glass, which means that you can move the glass around your factory and break out at a later stage,” Dave says. “And when you do, you’ll have a very clean break, and the stresses will be released. So, when you go onto subsequent processing, like toughening or edge polishing, then you don’t have chips or shelling in the glass edge causing stresses to be trapped in the glass, which might result in blown glass in the furnace.”
Silberschnitt V55 is the standard product for general glass cutting, including mirrored and low-e glass, and it has a standard evaporation time. Glass processors can choose to switch to Silberschnitt V59 for a longer evaporation time, or Silberschnitt V52 for a shorter evaporation time – usually required for cutting laminate and coated glass. For demanding shape-cutting, or for thicker glass, Silberschnitt W60 is recommended.
“The cost of our wheels and cutting fluid is very competitive,” Dave points out. “So, there are definitely opportunities to make savings, which will add up over a period of time.
“And if you’ve created edge stress in the glass – you’ve used the wrong degree of cutting angle on your cutting wheel, or used too high a pressure – then that could cause that piece of glass to blow when it goes through the tempering furnace.
“So there, you’re not talking about an incremental loss, you’re talking about a significant loss in terms of the cost of the glass, and the processing that you’ve already put into it.
“Hard science proves that if you use the right wheel, and the right cutting fluid, and the right cutting pressure, time and time again, you will significantly reduce your breakout and downstream wastage.”
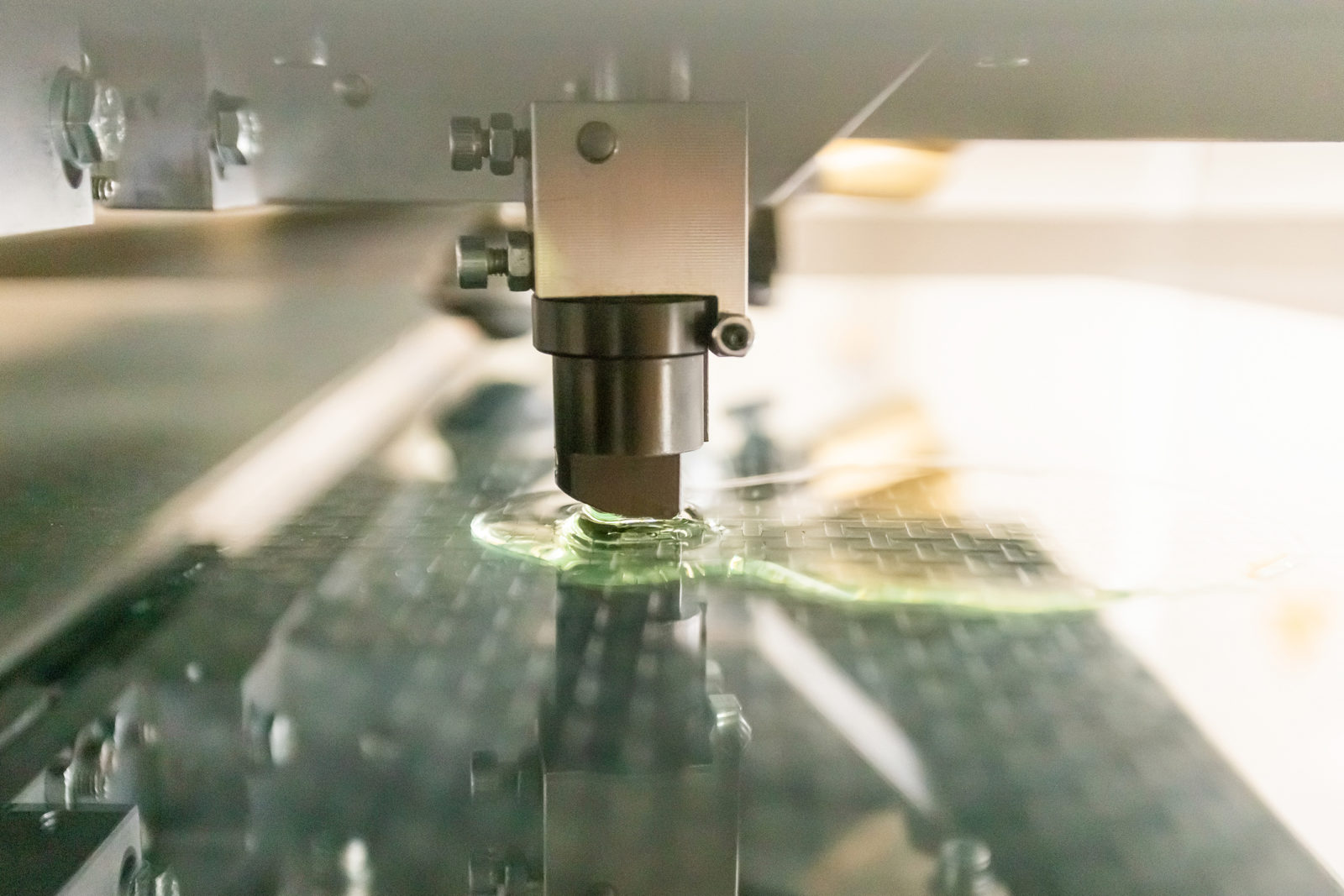