Fantastic plastic
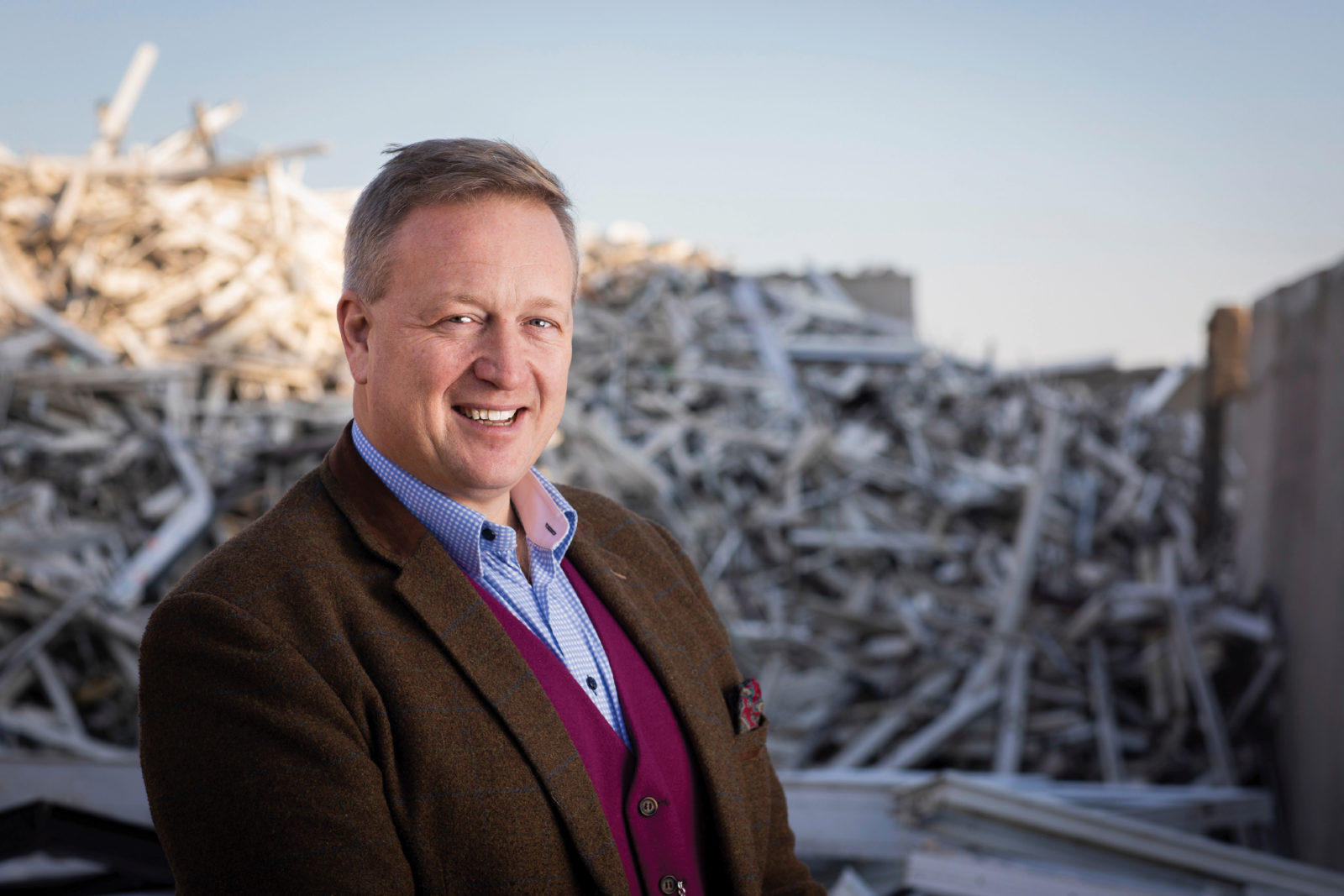
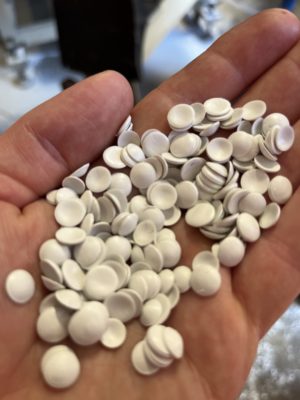
Glass Times editor, Luke Wood, visits Veka Recycling’s state of the art Wellingborough based facility; a £15 million operation that has been heralded as the most advanced in Europe.
There is plenty of evidence to suggest that, as consumers, we have become much more sensitive to sustainability.
A recent consumer survey from Deloitte found that 61% of consumers had reduced their usage of single use plastics during the pandemic, and nearly one in three claimed to have stopped purchasing certain brands or products because they had ethical or sustainability related concerns about them.
A large proportion of this applies to essential, everyday purchases but the glazing industry is also becoming much more switched on to the fact that sustainability sells. There is also a growing requirement for companies to demonstrate their green credentials as part of the supply chain, especially with commercial projects.
There are strong arguments for the sustainability of timber and aluminium but despite being ‘plastic’ PVC is also an incredibly green material – as evidenced by a number of co-extruded PVC systems (combining recycled with virgin polymer) as well as large scale recycling facilities.
Veka Recycling’s impressive operation, based in Wellingborough, is billed as the most advanced in Europe. Part of the Veka AG Group but operating independently from Veka’s extrusion business, Veka Recycling was originally established in the UK in Swanscombe, Kent, in 2007.
A decision was made to re-locate to a larger site with substantial investment secured to ensure it not only had the capacity to handle a greater volume of material, but that its processing was state of the art.
Constructed at a cost of £15 million, a figure that is said to be almost double the original budget and underlining the commitment from Veka AG to support the UK market (the decision to make the investment was actually made post-Brexit) the 5.5 acre Veka Recycling plant now has the potential to process up to 35,000 tonnes of post-consumer PVC frames and virgin offcuts.
The facility, which has been fully operational since 2021, is similar to two other sites built by Veka in Europe, one of which was constructed in Behringen, Germany in 1993 and the other was opened in France in 2006. The combined capacity of these plants has the potential to divert 100,000 tonnes of PVC windows away from landfill with the Wellingborough site representing the most sophisticated and modern processing of all three.
So much so that managing director, Simon Scholes, regards it as more of a production facility, rather than a recycling plant.
“We only process post-consumer PVC windows and PVC offcuts from fabricators,” he explains. “The Wellingborough plant was built from scratch to take advantage of the latest recycling technologies and we now produce the highest quality polymer for use in a range of products, including brand new window and doorframe profiles.
“We have the ability to promote and deliver PVC-U windows as truly sustainable at a time when plastic is under close scrutiny and to make the most of what is a tremendous resource.
“And of course, greater emphasis than ever is now placed on recycled PVC-U material following the supply chain issues that have hit the industry in recent times.
“The recent FIT Show provided considerable anecdotal evidence that homeowners now want to know that the PVC-U windows being removed from their homes will be dealt with sustainably,” he concluded. “This is gathering momentum, with more retailers now proactively advising homeowners that their old windows will be recycled.”