Ceramic ink printing onto glass
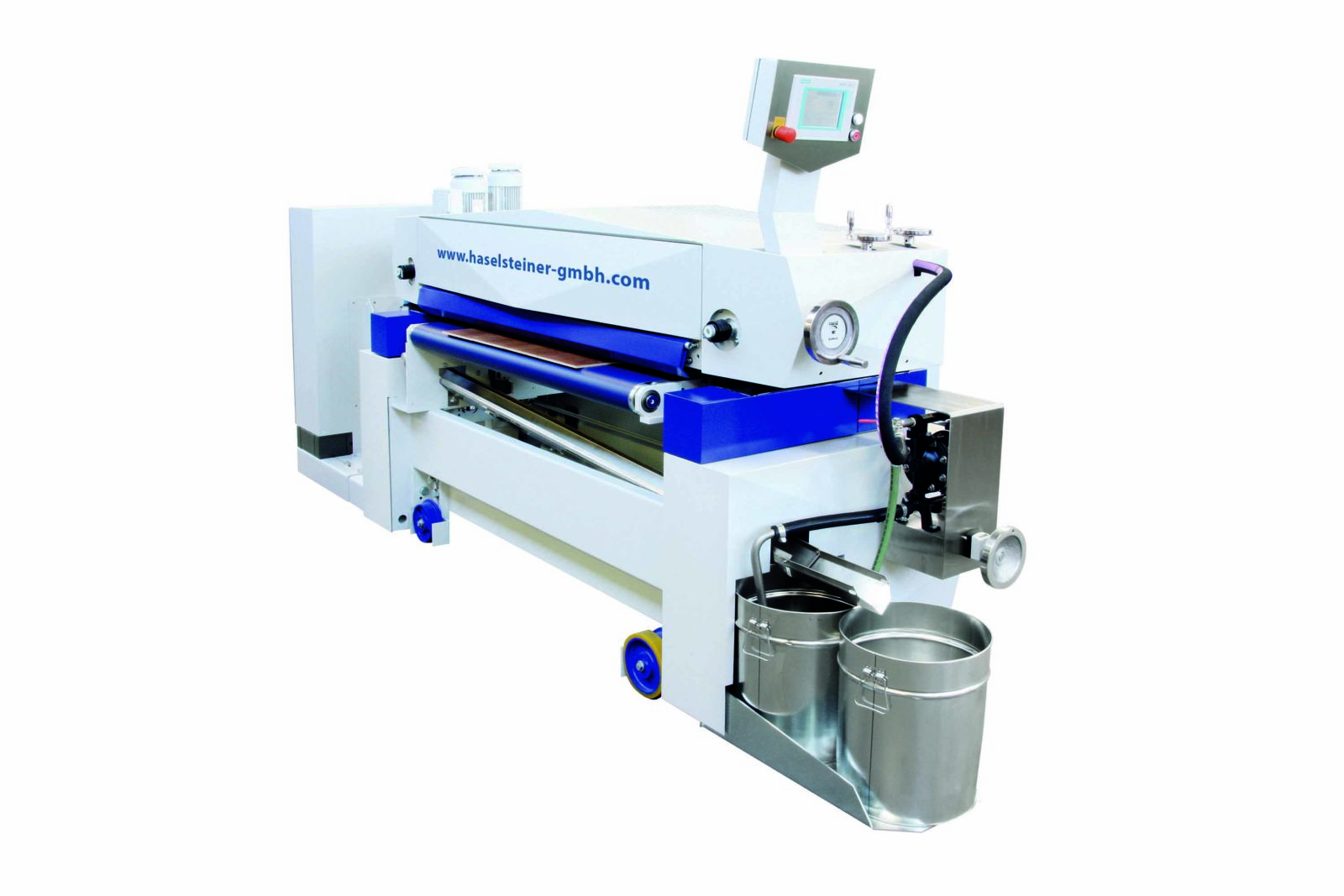
Flat Glass Solutions and Haselsteiner outline the merits of modern-day glass enamelling technology, especially using surface roller coater systems. Full surface and border (frame) roller coating can now be done at the touch of a screen.
Flat Glass Solutions has been appointed as an agent to Haselsteiner of Austria to bring ceramic ink printing equipment directly to the UK and Ireland.
Haselsteiner is a specialist manufacturer of glass decorating equipment for printing and drying with ceramic and organic colours. It offers a range of full-surface roll coaters, specialist border coaters, traditional silk screen printers, and infrared drying ovens.
Introducing automation and integrated manufacturing to these products means higher production output is achievable. Fourteen intelligent connections allow the highest efficiency at lowest production cost.
A new high-speed, full-surface roller coater and dryer has recently been installed at System 3 in Denton, Manchester. This roll coater and dryer means that production is massively increased as well as improving finished glass quality.
Allan Brown of System 3 said: “Roller coating glass for commercial applications is an integral part and a core product for us, and our previous 20-year-old system needed replacing. Having researched the options available, we chose the Haselsteiner roller coater because of the obvious engineering quality and the attention to detail in all aspects of the sale from Haselsteiner.
“The glass samples we saw were also the best produced.”
The new fully automatic FSC roll coater incorporates a large 305mm diameter, half tonne, pressure controlled roller system applying an even paint layer at 70 microns with a working width of 1.8m. The glass is automatically indexed to the coater and the precise electronically controlled ink application optimises the process.
For more than 20 years, Haselsteiner has supplied glass printing equipment to many of Europe’s largest glass companies, ranging from simple to fully automatic systems. Some of these systems have incorporated automatic paint recovery, screen cleaning and, more recently, the highly appraised border coating applicators.
Border coating glass has never been so easy: no masking up, no measuring, and colour paint change in less than 10 minutes.
The semi-automatic RRC 35 is highly efficient, has automatic adjustment for border width, and can even be used as a full surface applicator with multiple passes. A typical cycle time for a four-sided border coated glass lite of 1m2 is approximately five minutes.
Changes in paint width on the glass edges are automatically taken care of by the PLC control and user-friendly touchscreen. Colour changeover times are less than 10 minutes. In comparison with the alternative border coaters available on the market, the Haselsteiner system can demonstrate that: it is four to five times faster when border painting large glass; with a small footprint, it only requires one operator for the complete process; no heavy lifting or turning of large glass is necessary as the roller head can rotate through 360˚; different widths of border coating even on the same glass are possible and are taken care of automatically; full-face coating of glass on the machine is also possible regardless if size; automatic roller cleaning is available as an option; and paint application accuracy, regardless of glass length, is guaranteed.
Commercial glass suppliers are increasingly required to manufacture glass with painted borders and now, thanks to the Haselsteiner equipment available through Flat Glass Solutions, it is easily achievable. It is no longer extremely expensive and difficult to manufacture especially in large volumes.
Together, FGS and Haselsteiner can offer total support from planning to installation and total after-sales care.
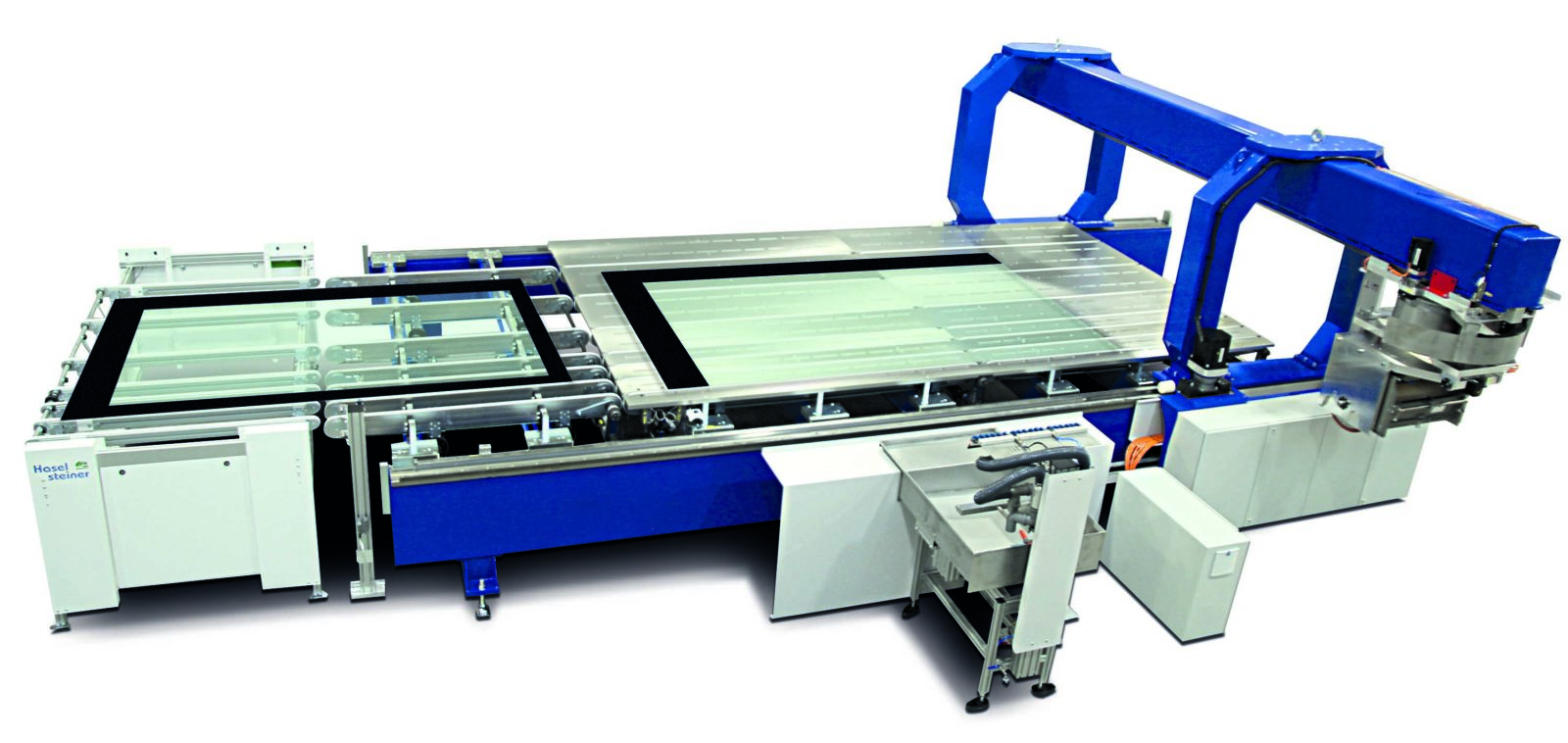