Behind the scenes at a fire safety glass test
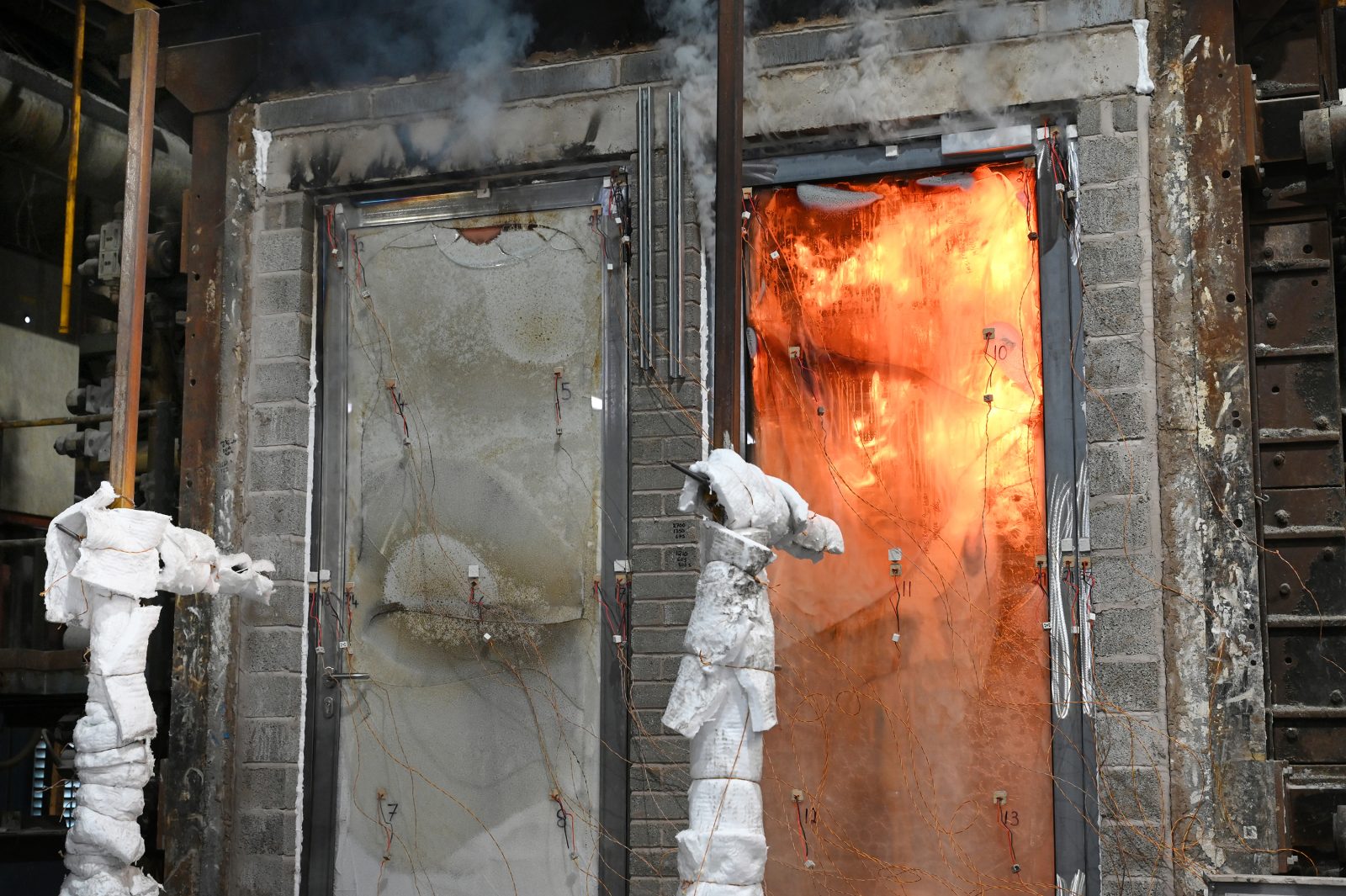
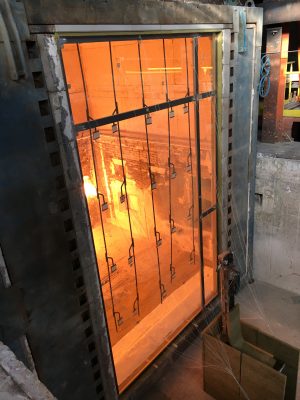
Certification is an integral part of the fire safety industry, ensuring that all products and systems meet the required regulations. But how is this test evidence created? Here, Dr Vince Crook, technical development director at Pyroguard, takes us ‘behind the scenes’ of a typical fire glass test.
When talking about fire safety glass, the conversation can focus on the building regulations, classifications and test data required, all ensuring that there is traceable evidence to back the specification of a particular system.
Fire tests form a vital part of this process, demonstrating that the system will perform as intended. However, there is far more to a fire glass test than a test report reveals, with weeks of preparation going into preparing for a test day.
Reasons for testing
There are several reasons for a test to be conducted: an Audit Test, Initial Type Test (ITT), a Scope Extension Test or a Project Specific Test. The Audit Test verifies that a manufacturer’s products are still up to standard and that there hasn’t been any change in materials or processes used. This is often a requirement from testing or certification bodies and can help manufacturers to maintain their test evidence, where required.
The ITT is the culmination of research and development work and is required for product launches, marking the first time that a new product is tested in an official laboratory. It is also the first step to CE and UKCA marking.
A Scope Extension Test is the most common, conducted to expand the range of applications or dimensions that a glazing system can be used in. It can take many different forms; from collaborating with a framing manufacturer to exploring other aspects of a system, such as new glazing medias or complementary products and counterpanes.
With architectural and built environment sectors in a state of constant evolution, glazing manufacturers are under pressure to continually push the boundaries of what’s possible.
Fire safety glass test: The preparation
One of the first steps when looking to undertake a scope extension test is to investigate what the current market requirements are for the area you wish to test. This can be used to set benchmarks for the test performance, with the aim to meet or even exceed the market requirements.
After this research has been completed the next step is to design the test itself, referring to the Test Standard and extended application rules to ensure all requirements are accounted for. Here, it is important to remember and reflect the real-world application of what you are testing for. For example, if a glazed partition is being tested, it would be beneficial to include both landscape and portrait panels to gain maximum benefit. Consideration of the support structure fixings is also essential, something that can often be overlooked and may lead to test constructions that cannot be replicated in the field. As a result of the myriad of market demands, multiple tests are often done to gain a useful scope.
Test day
The fire test is performed in an approved laboratory, with the installation and testing process overseen, and specimens inspected and surveyed by the testing body. The profiles are fabricated and installed in accordance with the approved system house design.
The glass, which has been pre-sampled, will be installed in the prepared frame, with care taken to ensure that the methods are practical for on-site installers. Finally, the entire construction is mounted onto a fire test furnace, with one side exposed to the fire and the entire system closely monitored throughout the test duration.
To measure the variety of different factors needed by the test standards for a valid fire test report, a series of wires and sensors are connected to the specimen. These monitor the surface temperature of the glass and frame, any deflection of the framing system and thermal-radiation levels. Any cracks or fissures that appear in the specimen are monitored by eye and a hand-held measurement gauge. For a test to be deemed a ‘pass’, it must achieve the specific thresholds set out by the relevant Test Standard.
How long is a fire safety glass test?
There is no set time limit, with a test continuing until the system fails completely in Integrity, Radiation and Insulation. As a result, a single system can often achieve multiple classifications from just a single test.
For example, if a system is being tested with EI30 glass, you would expect to see up to 30 minutes of heat protection, lowering the level of heat transmitted to the unexposed side. Whilst this is ongoing, the system may not fail on Integrity – the ability to prevent the passage of smoke and flame – for over an hour. As a result, this one test would result in the glazing system receiving both EI30 (Integrity and Insulation) and E60 (Integrity) classifications.
The cost
The cost of a fire safety glass test can vary between £9,000 and £20,000, and that is before considering the cost of the preparation, pre-test and the specimen itself. Testing is therefore a huge financial barrier to accessing the fire safety market and, given that the result isn’t guaranteed, is a risky exercise for smaller companies to embark upon.
Fire tests are just that: a test. There’s rarely a guaranteed outcome, as you aren’t just testing the glass but instead the glass and frame system as a whole, which can often be unpredictable. Fire tests are about furthering the development of glass and glazing systems and expanding their capabilities, continually pushing the boundaries of what is possible.